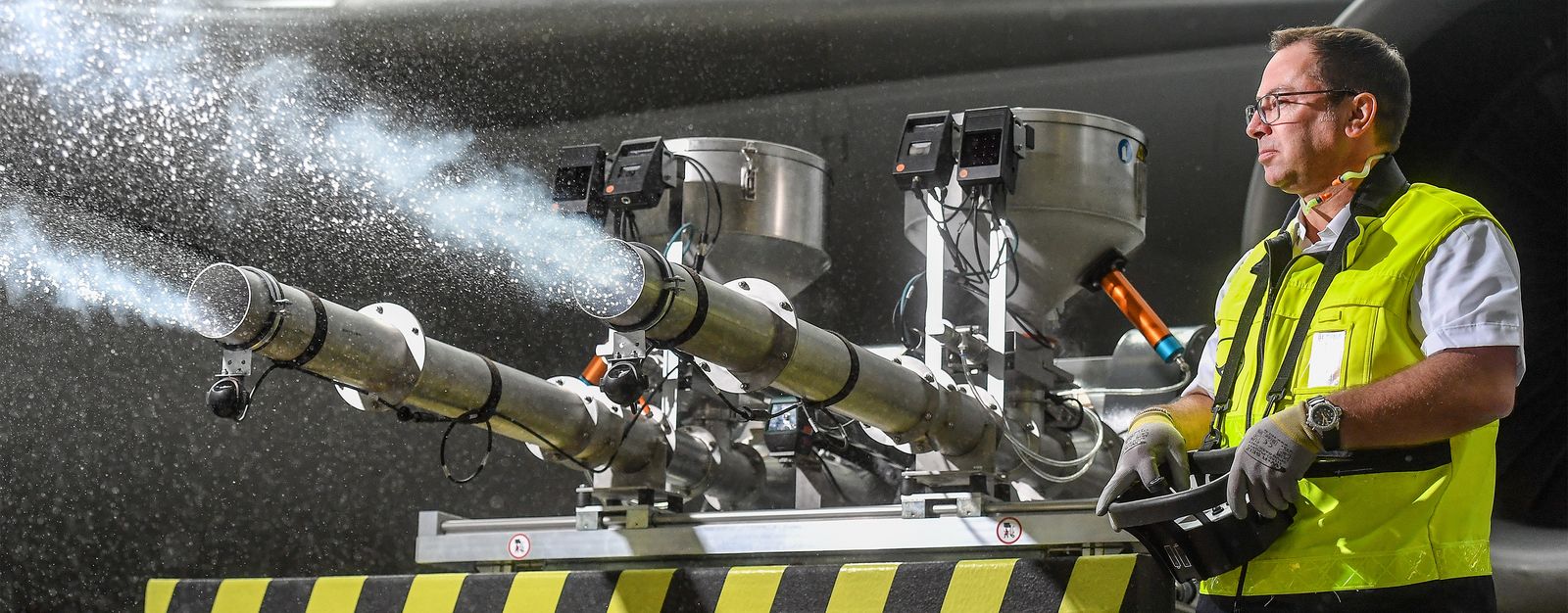
Wissenschaftler der h_da erarbeiten seit 2005 gemeinsam mit der Lufthansa Technik AG neue Prozeduren, um Flugzeugtriebwerke zu reinigen. Aus dieser Forschungskooperation ist schon das aktuelle Standardverfahren zur Triebwerkswäsche hervorgegangen. 2019 wird ein System in den Wartungsbetrieb eingeführt, das zusätzlich Treibstoff und Zeit einspart. Auf dem Campus in Darmstadt wird derweil schon an der Weiterentwicklung des Verfahrens getüftelt.
Dieses Geräusch! Unwillkürlich verlangsamen die drei jungen Studenten auf Höhe des Gebäudes C 18 ihren Schritt. Durch die offene Tür dringt ein beharrlich anschwellender Heulton. Er wird zum durchdringenden Dröhnen, das kurzzeitig sogar den Lärm der Tiefbauarbeiten auf dem benachbarten ehemaligen Verlagsgelände übertönt. Rudolf Kombeitz tritt nach draußen und schließt die Tür. Schlagartig sinkt der Lärmpegel auf ein erträgliches Maß. „Was ist das denn!?“, fragt einer der Studenten mit offenem Mund, als Kombeitz seinen Gehörschutz abgenommen hat. „Ein Flugzeugtriebwerk“, antwortet der lapidar. Beim Blick in die verdutzten Gesichter seiner Gegenüber huscht ein Grinsen über Kombeitz‘ Gesicht.
Thomas Zitzmann und Rudolf Kombeitz, wissenschaftliche Mitarbeiter am Fachbereich Maschinenbau und Kunststofftechnik, demonstrieren an diesem Vormittag in der Turbinenhalle (sie sprechen fachlich treffender von der Triebwerkshalle) die Ergebnisse ihrer Arbeit. Im Rahmen einer Kooperation mit der Lufthansa Technik AG arbeitet ihre Forschungsgruppe an „Verfahren zur Reinigung kommerzieller Fluggasttriebwerke“. Seit 2005 hat Professor Dr. Gerald Ruß mehrere Projekte zum Thema betreut. Der Spezialist für Kraft- und Arbeitsmaschinen und Wärmetechnik arbeitete früher unter anderem für einen Hersteller von Flugzeugtriebwerken. Nach seinem Wechsel an die h_da widmete er sich dem Problem, dass diese im Einsatz verschmutzen. „Staub, Pollen, Sand und Abgase lagern sich auf den Bauteilen an. Dadurch nehmen Aerodynamik und Wirkungsgrad ab, der Kerosinverbrauch steigt“, erläutert Ruß. Um dem gegenzusteuern, werden die Triebwerke mehrmals im Jahr grundgereinigt.
25 Kilometer von Wissenschaft zu Praxis
Den Grundstein zur Forschungskooperation legte eine Abschlussarbeit im Jahr 2005. „Damals hat unser Student Sebastian Giljohann den Ansatz eines wasserbasierten Verfahrens zur Triebwerksreinigung entwickelt“, sagt Gerald Ruß. Seither arbeiten Wissenschaftler und Studierende der h_da Hand in Hand mit Ingenieuren der Lufthansa Technik AG. Die Lufthansa-Tochter für MRO-Dienstleistungen – die Abkürzung steht für Maintenance, Repair and Overhaul, also Wartung, Reparatur und Überholung – unterhält am Frankfurter Flughafen einen wichtigen Standort. Was an der h_da berechnet, erprobt, getestet und analysiert wird, findet also nur 25 Kilometer nördlich in den großen Wartungshallen der Lufthansa Technik AG den Weg in die Anwendung.
„Sebastian Giljohann ist nach seinem Abschluss 2005 als Ingenieur zur Lufthansa Technik AG gegangen und hat dort unter anderem ein Innovationsteam aufgebaut“, berichtet Gerald Ruß. Lufthansa Technik nutzt das wasserbasierte Reinigungsverfahren seit 2007 unter dem Markennamen Cyclean®. Es ist heute Standard bei der Triebwerksreinigung, birgt jedoch Nachteile. Das verschmutzte Wasser muss entsorgt werden, seine im Triebwerk und den Leitungen der Anlage verbleibenden Reste können gefrieren. Deshalb kann das Verfahren weder im Winter noch in Permafrostregionen angewandt werden. Um diese Schattenseiten zu umfliegen, suchten h_da und Lufthansa Technik nach einem ganzjährig einsetzbaren, rückstandsfreien Reinigungsprozedere. 2010 rollten die Partner ein neues Projekt in Startposition: die Triebwerksreinigung mit gefrorenen Kohlenstoffdioxid-Partikeln.
Der Ansatz: Per Druckluft ins Triebwerk geschossene CO2-Pellets sollen die Verschmutzungen lösen – und praktisch im selben Moment in den gasförmigen Zustand übergehen. Dank einer Förderung des Bundesministeriums für Wirtschaft und Energie (BMWi) gewann das von der Lufthansa Technik geführte und von der h_da mit Forschungsleistungen unterstützte Projekt an Flughöhe. Zum Brennpunkt der Forschungsarbeit an der h_da wurde ab 2011 ein eigens dafür errichtetes Gebäude: C 18, Beiname Turbinenhalle. Gerald Ruß‘ gute Kontakte in die Branche hatten den Kauf eines Strahltriebwerks ermöglicht. Es war an einer Boeing 747-200 der chinesischen Fluggesellschaft Cathay Pacific im Einsatz, ehe es wegen eines Turbinenschadens ausrangiert wurde. In C 18 fand das Triebwerk seine neue Heimat.
Förderung auch für das Folgeprojekt
Nicht zuletzt aus den Fördermitteln des Bundes wurden ab 2014 zweieinhalb Mitarbeiterstellen finanziert. Eine davon hat Dr. Arthur Rudek inne. Er hatte seinen Bachelor an der h_da, dann seinen Master an der TU Darmstadt gemacht. Von dort kehrte er 2014 zurück. Als wissenschaftlicher Mitarbeiter von Gerald Ruß koordiniert und betreut Rudek die Arbeiten im Zusammenhang mit dem Triebwerk. „Das sind etwa vier bis sechs Abschlussarbeiten pro Jahr und noch mal so viele ingenieurstechnische Forschungsprojekte“, sagt er. Seit 2018 fördert das Bundeswirtschaftsministerium auch das nachfolgende Verbundprojekt von Lufthansa Technik und h_da. Für die Erforschung weiterer Triebwerksreinigungsmethoden fließen fast zwei Millionen Euro, davon gut die Hälfte an die h_da. Dieses Projekt beschäftigt Arthur Rudek noch bis 2022. Über technische Details darf er nicht sprechen. Verschwiegenheitspflicht.
Die cleane, anthrazitfarbene Fassade von C 18 passt zu den großen Erwartungen, die die Bezeichnung „Turbinenhalle“ weckt. Dabei ist die Halle eher hoch aufgeschossene Garage denn Hangar. Allenfalls der im Verhältnis sehr große Abluftschacht und die fast hallenhohen silbernen Tore deuten darauf hin, dass hier tatsächlich Großes vor sich geht. Das Aggregat des Herstellers General Electric vom Typ CF6-50 nimmt den Großteil des Raumes ein. An der Längsseite bleibt gerade genug Platz für einen Tisch mit zwei Rechnern und die Drucklufttechnik der Versuchsanlage. Schaltschränke, Werkzeug und Werkstattwagen beanspruchen die übrige Wandfläche. Das Triebwerk selbst ist 4,65 Meter lang, gut vier Tonnen schwer und hat einen Durchmesser von 2,44 Meter – das entspricht der Höhe eines Fußballtores.
Die demontierte Verkleidung gibt den Blick auf die einzelnen Triebwerksstufen frei: der Einlass mit dem Fan, Nieder- und Hochdruckverdichter, der Heißgasbereich mit der Brennkammer, Hochdruckturbine, Niederdruckturbine und Düse. Die Herausforderung, sagen die Forscher, bestehe darin, schwer zugängliche Bauteile zu erreichen und zu reinigen, ohne sie zu beschädigen. Die wenige Millimeter großen, mit Druckluft über eine Strahldüse ins Triebwerk geschossenen Trockeneispartikel zielen auf den Verdichtertrakt. Dessen erste Komponenten, die Schaufeln des Hochdruckverdichters, liegen etwa einen Meter hinter der Abschussstelle im Innern des Triebwerks. Davor befindet sich das von außen sichtbare, aus Schaufelblättern gebildete größte Gebläse, der Fan.
Kletterpartie am Schüsselrand
„Unser Reinigungsverfahren wird unter ‚On Wing‘-Bedingungen vorgenommen – das heißt, das Triebwerk wird dazu nicht vom Flügel abgenommen“, erklärt Rudolf Kombeitz. Auch wenn das CF6-50 an keiner Tragfläche hängt, muss er sich nun ganz schön strecken. Er ist über eine Leiter in den Triebwerkseinlass geklettert. Der gewölbte, weiß glänzende Ring erinnert an den Rand einer emaillierten Schüssel. Thomas Zitzmann schaufelt die Hagelkörner ähnelnden Trockeneispellets in einen Plastikeimer und reicht ihn Kombeitz nach oben. Der füllt das Trockeneis in den Metallbehälter der auf den Triebwerkseinlass zielenden Versuchsanlage. Das minus 78,5 Grad Celsius kalte Trockeneis lässt den Behälter binnen weniger Sekunden von außen vereisen. Jetzt klettert Kombeitz heraus, bringt Leiter, Eimer und Schaufel am Hallenrand in Sicherheit.
Ein Elektromotor, der an das Originalgetriebe angebaut wurde, startet das Triebwerk. „Er treibt die Hochdruckwelle an, bringt das Triebwerk bis auf etwa 2.000 Umdrehungen, rund 20 Prozent der Nenndrehzahl“, sagt Kombeitz. „Triebwerke werden grundsätzlich im sogenannten ‚Dry crank‘-Modus gereinigt, das heißt, es wird dabei kein Kerosin eingespritzt.“ Inzwischen hat die Niederdruckwelle eingesetzt. Das Heulen schwillt an. Jetzt heißt es: Feuer frei für CO2. Aus der Düse der Versuchsanlage schießt ein weißer Strahl. Am anderen Ende des Triebwerks tritt ein leichter Nebel aus. Sogwirkung, CO2-Konzentration und Lärm: Es wird Zeit, die Halle zu verlassen.
„Beim Auftreffen auf die Bauteile setzen die Trockeneispartikel kinetische Energie frei. Sie bewirkt im Zusammenspiel mit der Kälte, dass die Verschmutzungen sich zusammenziehen, verspröden und von den Komponenten lösen“, erklärt Arthur Rudek das Prinzip. Dass das Verfahren funktioniert, hätten die Versuche schnell gezeigt. „Die Wirkung ist ähnlich der eines Sandstrahlers, nur schonender.“ Und ohne Sand. Da die CO2-Pellets sofort in die Gasphase übergehen, ohne zuvor zu schmelzen, ist das Verfahren rückstandsfrei.
Analysen, Simulationen, Modellrechnungen
Die Tests am laufenden Triebwerk waren nur ein Baustein der Forschungsarbeit an der h_da. Zu Beginn des Projekts war analysiert worden, welche Bauteile wie verschmutzen. Verschiedene Reinigungsverfahren wurden zunächst an Einzelbauteilen getestet, aber auch am Computer simuliert und analysiert. „Wir haben die Parameter identifiziert, die die Effizienz der Reinigung beeinflussen“, erklärt Rudek. Zudem halfen die Wissenschaftler der h_da dabei, die Einbringungseinheit zu entwickeln sowie ein Konzept, das die Reinigungsmethoden mit Wasser und Trockeneis integriert. Parallel zu seiner Arbeit an der h_da hat Arthur Rudek bis 2018 am Dublin Institute of Technology (DIT) promoviert. Thema: „Entwicklung und Validierung eines numerischen Modells zur Simulation der CO2-Trockeneisreinigung von Fluggasttriebwerken.“ Darin analysierte er unter anderem das Zerfallsverhalten der Trockeneispartikel und entwickelte ein Verschmutzungserosionsmodell.
Inzwischen steht die Technologie kurz vor der Marktreife. Die Kooperationspartner haben eine mobile Strahlanlage konstruiert, die Kletterkünste und Leitern überflüssig macht. Die beiden Demonstratoren sind auf Montageplattformen mit omnidirektionalem Antrieb und höhenverstellbaren Scherenhubbühnen montiert. Dank ihrer Flexibilität sind die Anlagen für Triebwerke jeder Größe und Höhe geeignet. Die Konstruktion und das zugrundeliegende Verfahren hat sich Lufthansa Technik patentieren lassen. Ist die Einbringungseinheit per Fernbedienung in die gewünschte Position gebracht, werden die Trockeneispellets in den Verdichter geschossen. „Bislang wurden etwa 40 Triebwerkswäschen damit durchgeführt“, sagt Rudek. „Neun davon ‚on wing‘, also am realen Flugzeug durch Lufthansa Technik. Laut unserem Partner deutet alles darauf hin, dass die Methode bessere Ergebnisse liefert, als die wasserbasierte Reinigung.“ Mehrere Airlines hätten bereits Interesse an der Entwicklung signalisiert.
Nächste Station: Wartungsbetrieb
Die intensive Forschungs- und Entwicklungsarbeit hat alle ursprünglich gesteckten Ziele erreicht. Die Reinigung ist rückstandsfrei und damit von den Umgebungsbedingungen entkoppelt. Ein abschließendes Anfahren des Triebwerks zum Hinausbefördern von Schmutzwasser ist überflüssig. Das genutzte Kohlendioxid fällt als Abfallstoff bei der Rohölverarbeitung und in der Düngemittelindustrie an – der Reinigungsvorgang ist also CO2-neutral. Gegenüber früheren Reinigungsverfahren, für die das Triebwerk erst zerlegt werden musste, ist der Fortschritt ohnehin enorm. Nach rund 30 Minuten – deutlich schneller als bislang – ist das Aggregat wieder einsatzbereit. Damit ist die Trockeneisreinigung auch während kurzer Bodenzeiten möglich. Ein entscheidender Faktor in der unter hohem Konkurrenz- und Kostendruck stehenden Luftfahrtbranche.
Das Verfahren wird 2019 sukzessive in den Wartungsbetrieb des Unternehmens integriert und ergänzt die bewährte Triebwerkswäsche mit Wasser. „Unsere Arbeit zielt auf den Bestand“, unterstreicht Professor Gerald Ruß. „Sie sorgt dafür, dass die aktuell schon eingesetzten Triebwerke sauberer und sparsamer werden. Die höhere Effizienz steigert außerdem die Lebensdauer.“ Schon die wasserbasierte Reinigung senkte den Kraftstoffverbrauch spürbar. Die so gereinigten Triebwerke arbeiten effizienter, benötigen daher bei gleicher Leistung durchschnittlich ein Prozent weniger Kerosin. Das bedeutet einige hunderttausend Tonnen CO2-Emissionen weniger pro Jahr. Was nun mit Unterstützung der h_da Einzug in die Wartungshallen hält, verspricht also noch einmal erhebliche positive Effekte für Umwelt und Klima.
Autor
Daniel Timme
April 2019
Kontakt
Daniel Timme
Hochschulkommunikation
Tel.: +49.6151.16-37783
E-Mail: daniel.timme@h-da.de
Probebetrieb Wartung
Lufthansa Technik erprobt das Verfahren im Wartungsbetrieb mit einer mobilen Strahlanlage.