Materials Engineering
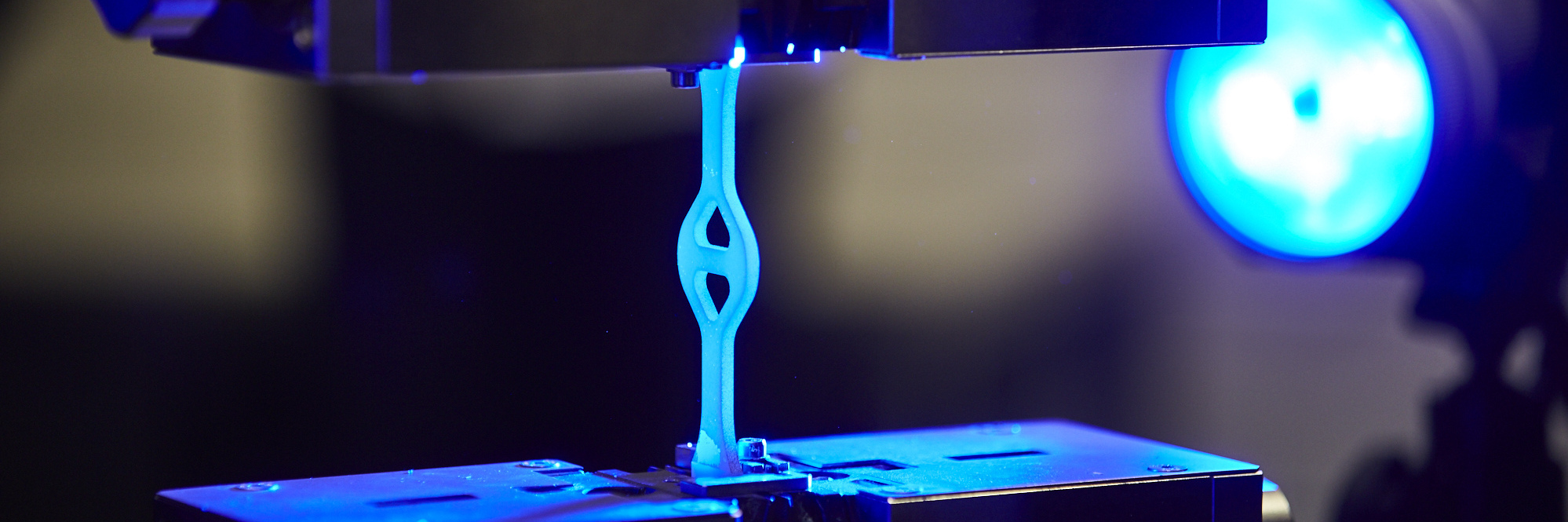
Several researchers from various disciplines at Darmstadt University of Applied Sciences (h_da) have joined forces at the Research Centre for Materials and Process Engineering (fz mpt), a research centre dedicated to materials and process engineering, to put the development of plastics and building materials on a new and more sustainable footing. The spectrum of applications ranges from ham packaging and sticky tape to aircraft components and civil engineering projects with lightweight concrete. The group has already received funding from the German Research Foundation (DFG) for international collaborations in this field. A joint project was commended by the State of Hesse as one of the best in the Distr@l funding programme.
By Christina Janssen, 6.3.2024
What do bottle caps and aircraft have in common? The bottle cap, in any case, will only fly if you throw it. However, both products are made of plastic: the cap from polypropylene and many parts of modern aircraft from ultralight composites. Our everyday lives are inconceivable without such plastics: surfboards and medical appliances, microchips and cheese packaging, aerospace components – the list is endless. “Wherever we look, we are surrounded by plastics,” says Dr Alexander Knieper from h_da’s Faculty of Mechanical and Plastics Engineering, putting it in a nutshell.
As plastics are clearly here to stay, researchers from three faculties at Darmstadt University of Applied Sciences have joined forces at the Research Centre for Materials and Process Engineering: mathematician Professor Romana Piat with her doctoral students Pascal Happ and Vinit Deshpande, plastics engineering experts Professor Martin Moneke, Professor Roger Weinlein and Dr Alexander Knieper, and civil engineer Professor Albrecht Gilka-Bötzow. Together, they are exploring ways to optimise plastics manufacturing and make value chains more sustainable. The group is also looking at building materials such as lightweight concrete. In essence, it’s about the virtual and numerical design of new materials. “We model new materials on the computer,” explains Professor Piat. In this way, it is largely possible to dispense with complex tests that would otherwise have to be conducted in the laboratory. “This saves time, material and energy.”
Harmless alternatives
In general, the objective when developing new materials is to optimise them for specific applications by mixing in additives. The mix must be spot-on, and the formula precisely adjusted to the respective application: adding fibres makes plastics stronger, metal particles make them conductive and UV blockers make them more durable. Plastics engineer Martin Moneke gives an example: “One of our last projects was concerned with substituting the white pigment titanium dioxide in a plastic because for some time it was suspected of being harmful to human health.” The aim was to improve the plastic’s mechanical properties at the same time. Here, Piat and Moneke experimented with particles of white chalk, which Granula Polymer, h_da’s cooperation partner, added to the plastic as a substitute. “In such cases, we use numerical models to simulate the behaviour of the new material mix on the computer and then predict its properties,” explains Romana Piat, who was a researcher at the Karlsruhe Institute of Technology (KIT) before joining h_da in 2015. To make such calculations, Piat and her team analysed the geometry of the individual plastic components with the help of microscopic and microtomographic images. “We ‘zoom’ into the material and take a close look at its microstructure. We are talking here about microparticles as fine as powder or fibres thinner than a human hair.”
But how close is simulation to reality? This is something that only the material tests in the plastics engineering labs at h_da can reveal. On the basis of the test results, the simulation model is then evaluated and improved, the blend of plastics is remixed and tested again in the laboratory. “We know the properties of the individual components beforehand, that is, rigidity, melting point, coarseness, particle size, and so on,” says Professor Gilka-Bötzow, explaining the procedure. “But it is not possible to predict exactly how these properties will change when individual components are mixed.” This interaction between repeated rounds of mathematical modelling and test series in the laboratory is how new materials are created.
Concrete blocks 2.0
An approach that can be transferred to building materials such as concrete. It is easy to picture a concrete block without recollecting the iconic scene from the film A Fish Called Wanda. The reason for turning the heavyweight into a lightweight has nothing to do with cinematic brutality, but with sustainability: “Nowadays, structural engineering has a wide range of alternative materials at its disposal,” says civil engineer Gilka-Bötzow. “However, that is not the case with civil engineering because these parts of the building are below ground level and come into contact with water. Here, there is virtually no alternative to concrete.” Every wooden high-rise therefore needs a concrete foundation.
The concrete should thus be lighter but nonetheless retain the necessary load-bearing capacity and durability. This means optimising, among other things, the aggregate in the concrete mixes – using similar methods as for plastics: “We humans see only the macro level, that is, the concrete block,” explains Gilka-Bötzow. “In the lab, we zoom into the concrete mixes, look at the micro, meso and macro level – and then combine simulations with laboratory tests.” In the past, many years often elapsed before new materials could finally be used in practice, say the researchers. Thanks to the combination of numerical mathematics and plastics engineering, the process can now be greatly accelerated.
Dating service for plastics
In other projects, the experts delve into the bag of tricks of plastics engineering to create very special plastic compounds: “For film packaging for ham or cheese, the sticky tapes on nappies or even certain automotive piping systems, plastic layers must be connected that in fact don’t like to mix – just like water and oil,” say Dr Alexander Knieper and Professor Roger Weinlein. Meant here are polypropylene and polyamide. To join them together to produce multi-layer films, the research team added polar compounds to the polypropylene layer. These act as “compatibilisers”, just as soap does for oil and water. “This creates an electrical charge on the surface so that the polyamide adheres to it,” explains Alexander Knieper.
The aim of another project conducted in cooperation with “Granula Polymer GmbH”, a family-owned company in Groß-Umstadt in Hesse, was to combine polypropylene and polyamide to form components that unite the respective advantages of the two polymers. In this case, a reactive substance that bonds with the polyamide was added to the polypropylene. This created strong bonds at the interface, enabling a combination of the two different “plastics”.
Professor Piat, Pascal Happ and Vinit Deshpande made a digital twin of the test objects produced in this way. “First of all, we tested whether our simulation mirrors how the material behaves in reality,” reports doctoral student Pascal Happ. In the next steps, the team was able to simulate how the mechanical properties of the composite material are changed by making individual adjustments and altering the formula. “Our aim here is also to achieve faster and more sustainable results,” summarises plastics expert Weinlein.
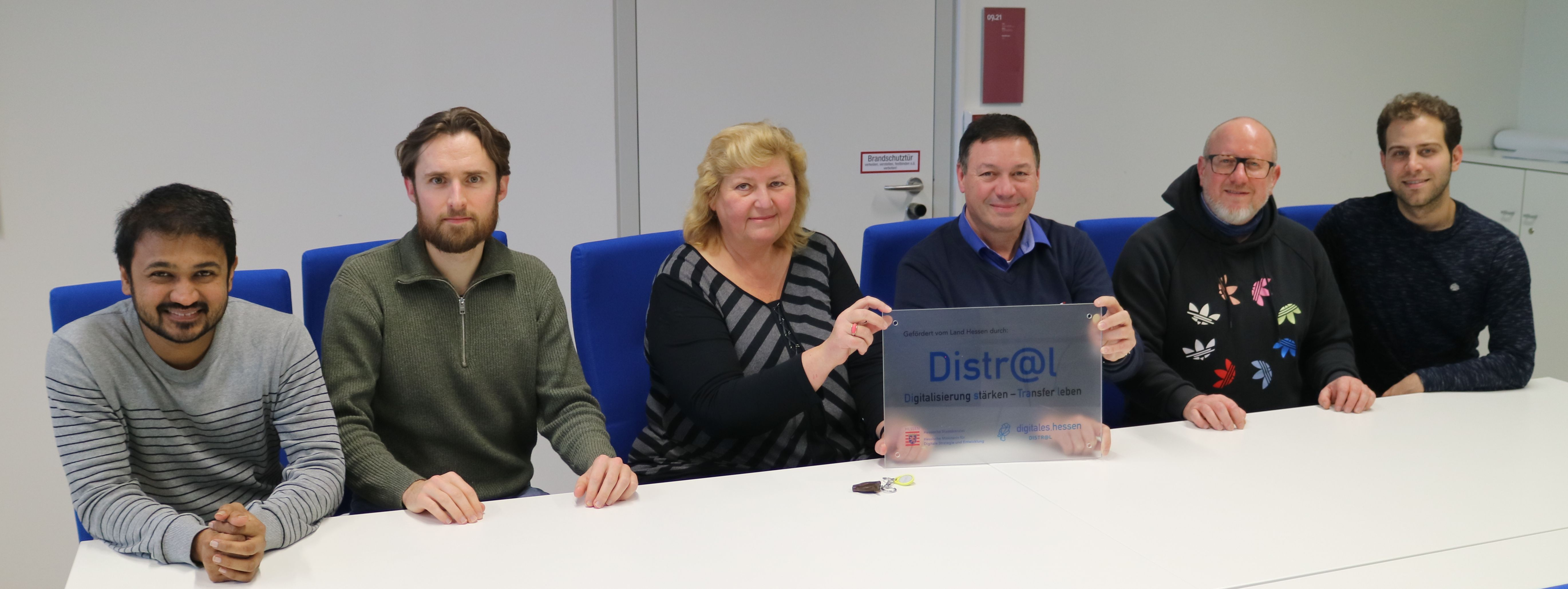
Such collaborations are of great benefit for the project partners from industry. “In general, manufacturing companies don’t have their own modelling or numerics specialists,” explains Romana Piat. “That is why we designed our software to be very user-friendly.” This means in practice that the company is given a selection of materials and then uses the software to predict which of them might be a good match. A kind of dating service for plastics. The project was funded by the Hessian Ministry for Digital Strategy and Innovation within the Distr@l programme and awarded the “Gold” quality seal in the final evaluation.
New international partnerships
To put its joint research work on a broader footing, the h_da team is endeavouring to network more on the international level. As part of a project funded by the German Research Foundation (DFG) and aimed at establishing international collaborations, Romana Piat organised a top-level workshop in the winter with participants from Germany, the US and Scotland. The meeting in Darmstadt, which was co-financed by h_da’s Research Centre for Materials and Process Engineering, was the starting point for joint projects at the international level: the group wants to intensify the exchange of expertise and is currently planning further workshops and some first joint proposals for externally funded projects.
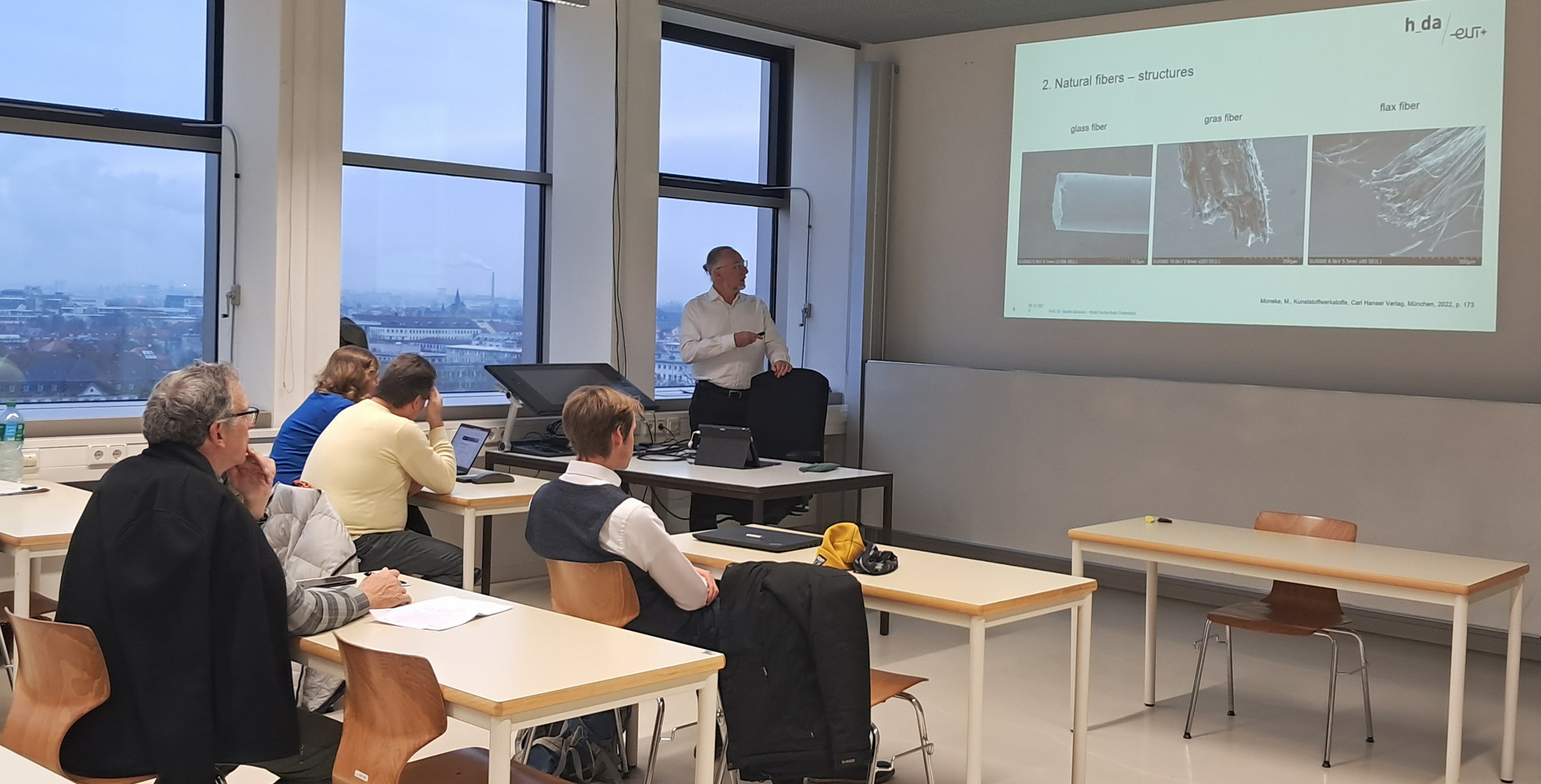
Students, too, should benefit from this. The scientists also want to use exciting research projects to arouse curiosity and enthusiasm for their subject. After all, there is an urgent demand for plastics engineering, mathematics and civil engineering graduates on the labour market – and, at least for the time being, they do not need to worry about AI threatening their jobs.
Contact
Christina Janssen
Science Editor
University Communication
Tel.: +49.6151.533-60112
Email: christina.janssen@h-da.de
Translation: Sharon Oranski
Further information on the study programmes
h_da research team
Professor Gilka-Bötzow’s website
Professor Martin Moneke on LinkedIn
Professor Romana Piat’s website
Professor Roger Weinlein’s website
Dr Alexander Knieper
Pascal Alexander Happ
Vinit Vijay Deshpande