Innovative composites created on the computer
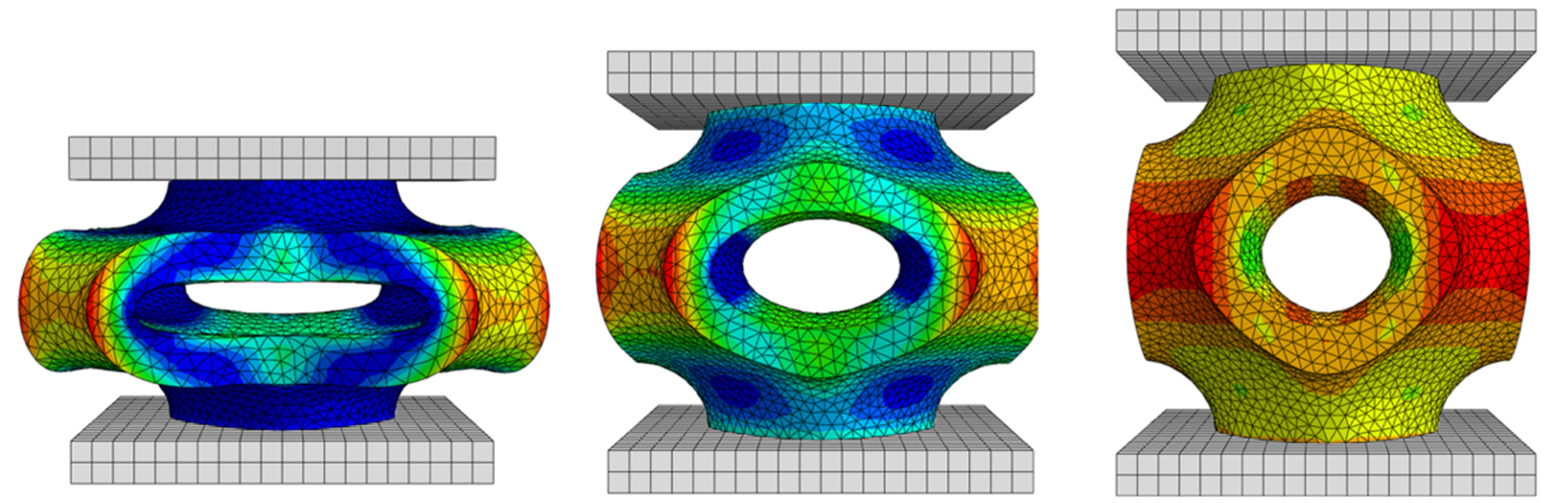
Composites made of carbon fibres, ceramic particles or metal? Optimised through numerical microstructure design? Which promising new composites can be created when scientists from numerical mathematics and materials research put their heads together can now be seen in several interdisciplinary research projects at Darmstadt University of Applied Sciences. What’s special about it? The fact that that they are not developing the materials in the laboratory, but on the computer.
By Astrid Ludwig, 18.7.2023
In the composites industry, new compositions or material mixtures generally need a lengthy development time before they are ready for use. It requires years of experience and extensive testing before a new product can be launched on the market. This demands time, money, people and resources. “This approach is very complex and also involves a lot of material waste,” says Romana Piat, Professor of Numerical Mathematics at h_da’s Faculty of Mathematics and Natural Sciences. “It’s costly and unsustainable,” she adds. Her research group is currently working in interdisciplinary teams at Darmstadt University of Applied Sciences to potentially change this in the future.
They are experimenting with a digital technology for use in the materials development process. “We’re attempting to develop materials on the computer,” explains Professor Piat. The researchers control and simulate processes and tests on the computer that otherwise take place in the laboratory. In the future, this could not only shorten industrial processes and make them more eco-friendly by significantly reducing material and energy consumption but also pave the way for entirely new products and applications.
Interdisciplinary teams
With this goal in mind, researchers, students and doctoral candidates from h_da’s Faculty of Mathematics and Natural Sciences have joined forces with colleagues from its Faculty of Mechanical and Plastics Engineering. In their search for new digital approaches to create innovative materials, they are collaborating on several research projects with partner universities, such as the University of Augsburg and the Technical University of Braunschweig, and companies from the plastics industry, including the family-owned company “Granula Polymer GmbH” in Gross-Umstadt in Hesse.
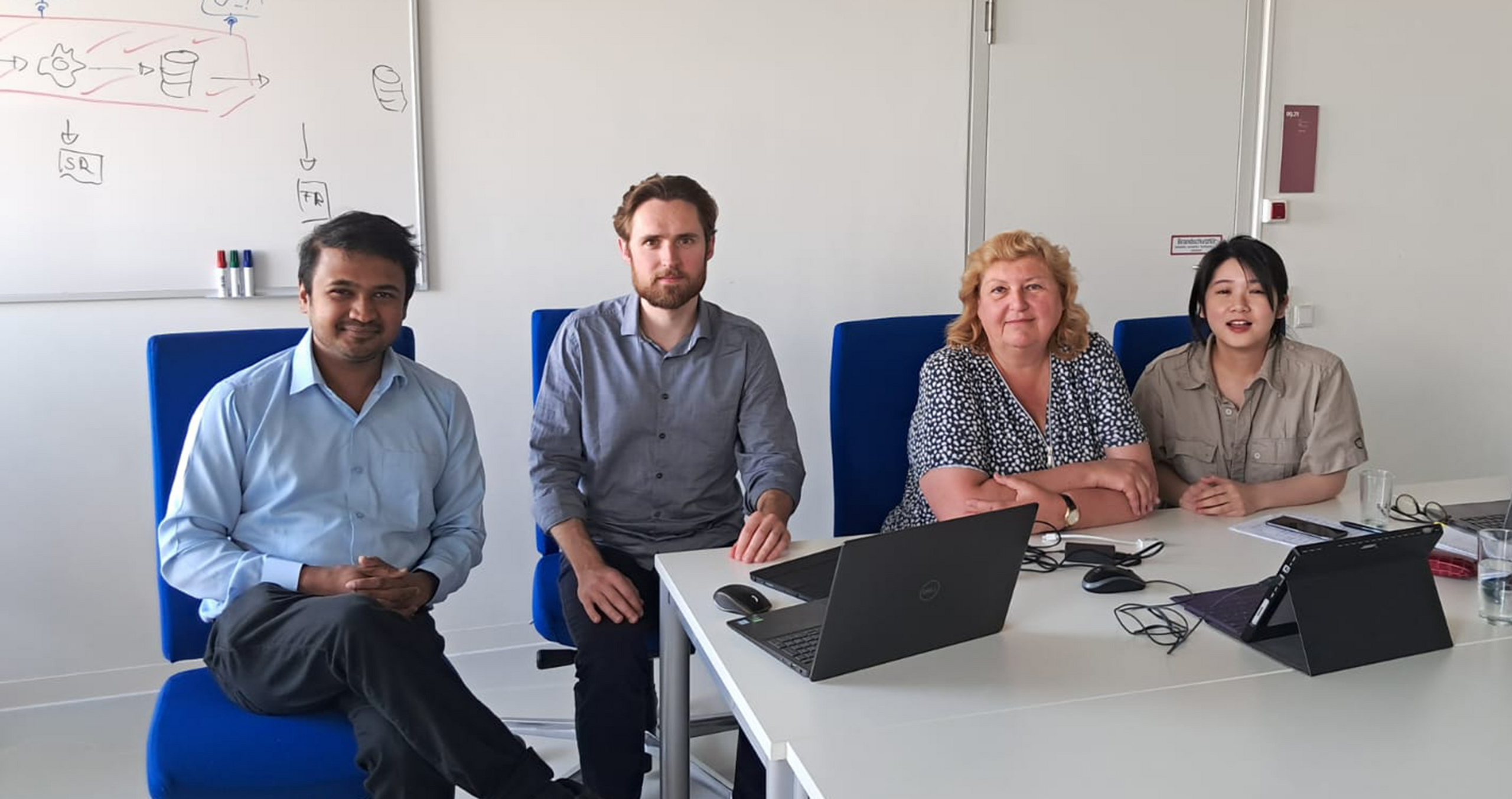
Professor Piat reports that particle- or fibre-reinforced composites are found in the automotive and aerospace industries as well as in products or household items for everyday use, and are mostly customised for specific applications. For example, carbon fibre- or ceramic-reinforced composites have long been used in the automotive industry as well as space or satellite technology because they are particularly lightweight, heat-resistant and robust.
Sensitive sensors
Romana Piat, who previously worked at KIT (Karlsruhe Institute of Technology) and has been teaching at Darmstadt University of Applied Sciences since 2015, has been examining how mathematical and digital methods can be applied in the development and optimisation of new materials for many years. It is possible to develop an optimised microstructure design on the computer which is customised to the application in question. In this way, for example, precise and compact components can be designed and endowed with additional properties, says Pascal Alexander Happ, a mechanical engineer studying for his doctoral degree at h_da. In the framework of a research project, he is currently dealing with the electrical conductivity of composites, which is important for sensory applications, among other things. Within Professor Piat’s interdisciplinary team, Happ is examining “how the microstructure needs to look in order to ensure better conductivity.” He uses numerical methods to do this.
Verification through lab tests
Plastics, which are non-conductive but easily mouldable and do not degrade, are combined with conductive materials such as carbon fibre or metal. Happ is working on software that monitors the behaviour of the electrical resistances and developing algorithms that calculate the optimal distribution of additives within the microstructure. This distribution, he explains, depends on the type of particle. The particles can be spherical, elongated or with irregular shape in appearance. “The aim is to design a chain along which the electrical current can flow.” The flow of electrical current within the material’s microstructure can then be finely steered via these conducting paths or conductive channels. He explains that sensitive sensors are important for monitoring the load on components, for example.
“We already know that our results are correct,” Romana Piat and Pascal Alexander Happ are pleased to say. The h_da team’s digital results were verified in the laboratory and compared with experimental results. “It’s important that our numerical predictions of composite properties are correct,” stresses Professor Piat. “That is why our cooperation partners produce samples to verify experimentally how good our computer simulations are.”
Design for 3D-printable components
Thi Ngoc Diep Tran, a mathematician at h_da, is working on a research project in which the periodic structure of a unit cell is represented with a mathematical equation. Through the distribution of such unit cells, it is possible to form a lattice structure as required. The aim, she says, is to construct a component from this which can then be produced with a 3D printer. Thi Ngoc Diep Tran is responsible for designing and calculating the microstructure, which she plans to further optimise on the computer with the help of artificial intelligence. “The 3D printer then uses the data I’ve generated,” she explains. In this way, and in cooperation with the University of Augsburg, a printable aeronautical turbine made of a new composite should result that unites the properties of very hard ceramics and malleable, liquid metal. “We’re still at a very early stage,” says Thi Ngoc Diep Tran. The researchers have submitted the project to the German Research Foundation for funding.
New applications in medicine
Vinit Vijay Deshpande, who is writing his doctoral thesis at the Faculty of Mathematics and Natural Sciences at h_da, is working on mathematical models for ceramic foams. Such foams are often used as insulating material or in lightweight constructions. As a heat-resistant, inexpensive and high-performance material, it is also used in the automotive industry in catalytic converters. Vinit Vijay Deshpande’s research centres on porous ceramic foams with a cell-like structure. He reproduces this foam structure on the computer and simulates how it reacts to mechanical pressure as well as how it deforms and absorbs energy. “This is important for crash tests,” he explains as an example.
Foam ceramics are playing an increasingly important role in high-tech applications. Space agencies use the material for heat shields on satellites or spacecraft. But porous ceramic foam, as Vinit Vijay Deshpande explains, could also have promising applications in medicine and biomedicine. “It’s possible to customise the material very quickly to individual patients.” A possible application, for example, could be biomedical implants. The porous cells of the ceramic structure can fuse with human cells, thus offering a stable alternative and a substitute for the steel and titanium implants used to date.
“The material is at the development stage,” says Professor Romana Piat. She is convinced: “What we’re doing here is interdisciplinary and at the interface between applied and fundamental research.”
Contact
Christina Janssen
Science Editor
University Communication
Tel.: +49.6151.533-60112
Email: christina.janssen@h-da.da
Translation: Sharon Oranski
More information about the PZAI: pzai.de/