Mikroreaktoren: Effizienter, sicherer, nachhaltiger
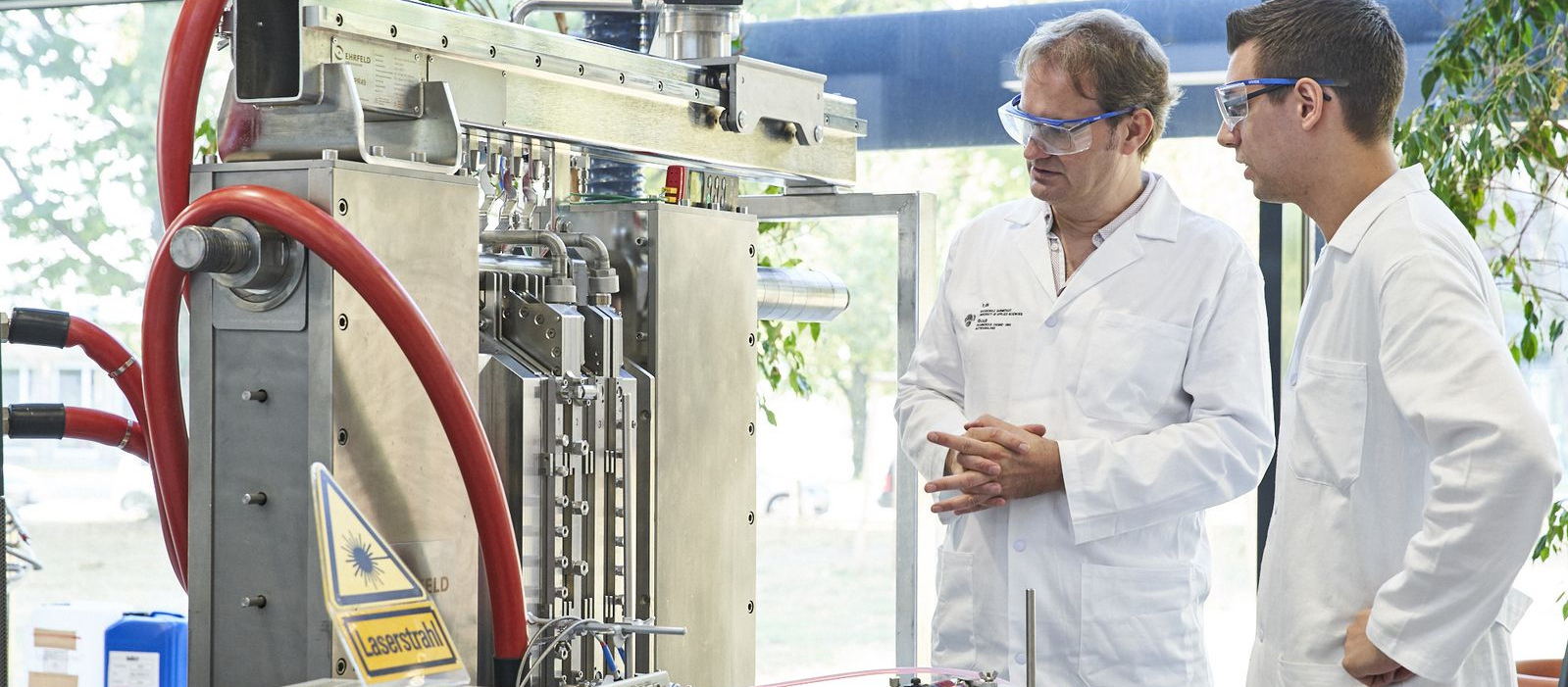
Die Herstellung von Medikamenten und Chemikalien ist ein hochkomplizierter Prozess, bei dem Unternehmen in puncto Qualität und Sicherheit höchsten Standards gerecht werden müssen. Für die chemische Produktion von Medikamenten wie Krebstherapeutika sind zahlreiche Teilschritte in verschiedenen technischen Apparaturen nötig, bis am Ende der gewünschte Wirkstoff entsteht. Am Fachbereich Chemie- und Biotechnologie der h_da forscht Prof. Dr. Frank Schael an einer Technologie, mit der solche Prozesse effizienter und sicherer vonstattengehen könnten. „Mikroverfahrenstechnik“ lautet der Schlüsselbegriff: Technologie im Mikro-Maßstab – und mit enormer Leistungsfähigkeit.
Von Christina Janssen, 11.11.2018
Die Chemie muss stimmen. Doch tut sie es auch? Patrick Rojahn, wissenschaftlicher Mitarbeiter am Fachbereich Chemie- und Biotechnologie, und Masterstudent Oliver Ruß stehen im lichtdurchfluteten Technikum vor einer hohen Stahl-Apparatur und diskutieren den Versuchsaufbau. Das aus Metallplatten, Rohren und Schläuchen bestehende Gebilde ist ein Produktionsreaktor, mit dem chemische Substanzen hergestellt werden können – zum Beispiel Wirkstoffe für Medikamente.
Hier brodelt, knallt und stinkt es nicht, wie es das Chemie-Klischee vielleicht erwarten lässt. Am Arbeitsplatz der Nachwuchsforscher Rojahn und Ruß ist Hightech angesagt. Die beiden sind gerade dabei, durch feine Schläuche pink eingefärbtes Wasser in den Reaktor zu pumpen. „Wir wollen herausfinden, wie gleichmäßig diese Testsubstanz durch die Anlage strömt“, erklärt Rojahn. „Außerdem möchten wir Druck und Temperatur sehr genau konstant halten.“
Die hochmoderne Anlage hat einen Wert im sechsstelligen Euro-Bereich und wurde der h_da vom Kooperationspartner Ehrfeld Mikrotechnik GmbH aus Rheinland-Pfalz zu Forschungszwecken zur Verfügung gestellt. Nicht ganz uneigennützig, versteht sich: Ein Team um Prof. Dr. Frank Schael soll herausfinden, unter welchen Bedingungen komplizierte chemische Reaktionen in der hochmodernen Apparatur optimal ablaufen.
Hightech in winzigen Dimensionen
Das ist alles andere als trivial: Im Inneren jeder Stahlplatte stecken Reaktoren, die aus winzigen Bauelementen bestehen. Jeder einzelne davon ist bei einer komplexen chemischen Reaktion für eine bestimmte Aufgabe zuständig. Das heißt stark vereinfacht: Man pumpt die Substanzen A, B und C in den Reaktor hinein und bekommt am Ende die erwünschte Substanz D heraus, beispielsweise einen Wirkstoff wie Ibuprofen. In der klassischen „Kesselchemie“ braucht es dafür oft viele Teilschritte in unterschiedlichen Apparaturen. Die Plattenreaktoranlage schafft das dagegen in einem Durchlauf, ohne dass irgendwer zwischendurch Hand anlegen muss. Im Idealfall. Und der ist auch im Leben eines Chemikers nicht einfach zu haben, denn das Zusammenspiel von Technik und Chemie kann herausfordern: „Wir sprechen hier von einigen Millimeter bis – im Laborversuch – 25 Mikrometer feinen Strukturen im Inneren der Reaktoren“, erläutert Schael. „Zum Vergleich: Ein menschliches Haar hat einen Durchmesser von etwa 80 Mikrometern.“ Aber gerade so kann das Geschehen im Reaktor exakt kontrolliert werden. Strömungsgeschwindigkeit, Vermischung, Temperatur, Druck, Rezeptur – das Zusammenspiel zahlreicher Parameter will der Experte für Mikroverfahrenstechnik mit seinem Team untersuchen. „Mit so leistungsstarken Mikroreaktoranlagen wird an Hochschulen oder Universitäten normalerweise nicht gearbeitet. Wir müssen den Reaktor daher erst einmal kennenlernen, um dann das Potenzial für neue Prozesse auszuloten“, erläutert Patrick Rojahn. „Dazu haben wir eine eigene Lasermesstechnik entwickelt und an den Reaktor angeschlossen.“
Mehr Sicherheit, weniger Energieverbrauch
Das wuchtige Äußere der Apparatur ist also nur die Hülle, die die Mikro-Technik im Inneren robust macht für den anspruchsvollen Einsatzort in einer chemischen Fabrik. Umso erstaunlicher: Die Mikroreaktoren können es, in manchen Bereichen, durchaus mit einer großchemischen Produktionsanlage aufnehmen. Schon heute werden verschiedene Vorprodukte für Arzneimittel mit dieser neuen Technologie produziert. Die Vorteile liegen nach Schaels Einschätzung auf der Hand: mehr Sicherheit, mehr Effizienz, weniger Energie- und Ressourcenverbrauch. Da in den Mikroreaktoren mit geringen Mengen gearbeitet wird, sinkt das Risiko etwa bei Synthesen mit gefährlichen Stoffen wie konzentrierten Säuren oder metallhaltigen organischen Verbindungen. Die entstehende Wärme kann besser abgeleitet werden als aus einem Kessel mit großem Volumen und vergleichsweise kleiner Oberfläche. Und auch die Vermischung der Chemikalien verläuft im Mikroreaktor effektiver. „Stellen Sie sich einen Kessel über zwei Gebäudeetagen vor, in dem Substanzen mit einem großen Propeller gemischt werden“, erläutert Schael. „Da kann es gut sein, dass rechts oben im Kessel etwas ganz anderes passiert als links unten.“ Im Mikroreaktor sind die Vorgänge insgesamt viel besser steuerbar – ein wichtiger Faktor in der chemischen Produktion. Trotzdem muss am Idealfall noch gearbeitet werden. Ein Problem, an dem die Mikroverfahrenstechnik mitunter krankt: Die schmalen Kanäle neigen zu Verstopfung. Deshalb funktionieren die Reaktoren nur mit „sauberen“ Flüssigkeiten, die nicht durch Partikel verunreinigt sind. Zudem kann es – wie so häufig in der Chemie – auch in den Mikroreaktoren zu „Nebenwirkungen“ kommen. Das heißt: Unter Umständen bilden sich unerwünschte Nebenprodukte. Dieses Risiko wird durch die Mikroverfahrenstechnik im Vergleich zu konventionellen Methoden allerdings minimiert, weil man die Abläufe im Reaktor extrem präzise steuern kann.
Forschungsprojekte mit praktischem Nutzen
All diesen Phänomenen wollen Schael und sein Team in den kommenden Jahren auf den Grund gehen. Die Forschung am Produktionsreaktor ist Teil des groß angelegten Transferprojekts s:ne – Systeminnovationen für Nachhaltige Entwicklung der h_da. Konkret geht es um die Herstellung von Lederchemikalien – eine ganze Palette an Substanzen zum Gerben und Färben, Enthaaren und Entfetten, Weichmachen und Imprägnieren.
„Immer wieder gibt es Berichte über Chemikalien in Schuhen oder anderen Lederprodukten, die da nicht hineingehören“, beschreibt Professor Schael die Ausgangslage. „Dann stellt man sich die Frage, wie das geschehen kann – ob es an Lederchemikalien minderer Qualität liegt oder an unkontrollierten Reaktionen bei der Lederherstellung.“ Ein wichtiges Thema für viele Verbraucher, schließlich kommen wir fast täglich mit Schuhen, Taschen oder Autositzen aus Leder in Kontakt. „Zwar gehören deutsche Lederhersteller zu den saubersten und effizientesten der Welt, doch der Großteil der Ware wird im Ausland in kleineren Betrieben hergestellt, die oft nicht auf modernstem Stand arbeiten. Die Forschung am Mikroreaktor soll dazu beitragen, solche Herstellungsprozesse sicherer und effizienter zu machen.“
Auch für die beteiligten Mitarbeiter und Studierenden ist der praktische Nutzen eine Motivation: „Wir arbeiten hier an Wissen, das für Unternehmen enorm hilfreich ist und das wir dann zur Verfügung stellen können“, sagt Patrick Rojahn. Ein Transferprojekt im besten Sinne also: Der Erkenntnisgewinn aus der Forschung wird direkt in die Praxis übertragen. Für Masterstudent Oliver Ruß ist das eine völlig neue Erfahrung: „Es ist toll, wenn man als Student echte Werte generieren kann. Das macht Spaß und ist etwas ganz anderes, als in einer Vorlesung zu sitzen.“
Im Labor nebenan sind gerade zwei weitere Masterstudierende bei der Arbeit. Malte Naujoks und Pascal Plösser bereiten Messungen an einem Mikroreaktor vor, der im Vergleich zu seinem „großen Bruder“ aus dem Technikum eher unscheinbar daherkommt: Eine Metallplatte mit würfelförmigen Strukturen darauf, auch hier Schläuche und Messgeräte, viel mehr ist nicht zu sehen. Dennoch steht dieser Reaktor im Schuhschachtelformat für die zweite Forschungslinie im Bereich Mikroverfahrenstechnik an der Hochschule Darmstadt: „Man kann solche Reaktoren auch als Werkzeuge einsetzen, um chemische Reaktionen für die Übertragung in den technischen Maßstab zu optimieren“, berichtet Frank Schael. Zuletzt hat sein Team eine sogenannte „Henry-Reaktion“ untersucht, die unter anderem bei der Herstellung von Antibiotika eine Rolle spielt. Das sind große Moleküle, die chemisch oft über zahlreiche Schritte mit entsprechend vielen Zwischenprodukten synthetisiert werden. „Wir arbeiten in diesem Reaktor mit Modellsubstanzen, um herauszufinden, an welchen Stellen die Synthese optimiert werden könnte.“
Paradigmenwechsel in den Unternehmen
Malte Naujoks und Pascal Plösser untersuchen gerade ein circa vier mal vier Zentimeter kleines Kunststoffplättchen, das von hauchdünnen Kanälen durchzogen ist. Von diesen winzigen „Chiplaboren“ haben die beiden Studenten am Bildschirm verschiedene Varianten entwickelt und im 3D-Drucker ausgedruckt, um sie zu testen. Zunächst werden nun die Leitungen des Reaktors gespült, dann die Reagenzien hineingepumpt. Durch die Kanäle im Chip laufen die Chemikalien in eine winzige Reaktionskammer, in der sie sich vermischen und miteinander reagieren. Die Anlage surrt ein wenig wie ein Kopiergerät – und nun wird es spannend. Stimmt die Chemie – oder stimmt sie nicht? Nach wenigen Augenblicken verfärbt sich die Flüssigkeit in einem kleinen Schlauch am Reaktor gelb. Naujoks und Plösser sind zufrieden: Die Farbe stammt vom Jod, das bei der gerade durchgeführten Reaktion tatsächlich entstehen soll. Wie viel es ist, wird mit einem Spektrometer gemessen. Über einen Kontrollbildschirm zittern rote Kurvenverläufe, die am Ende zu einer endgültigen Messkurve erstarren. Diese wird nun exakt analysiert. Welche Stellschrauben müssen weiter gedreht werden, um die Reaktion zu optimieren…? Es bleibt noch viel zu erforschen.
Mancherorts wo es heute noch in Kesseln dampft und brodelt, könnten schon bald Mikroreaktoren die Arbeit verrichten, da ist sich Professor Frank Schael sicher. Viele große Pharma- und Chemieunternehmen beschäftigen sich inzwischen mit diesem Thema. Doch die Mikroverfahrenstechnik wird vorerst etwas für anspruchsvolle Fälle bleiben, meint Professor Schael. Denn die Umstellung von den traditionellen Kesselverfahren – die Chemiker nennen das „Batch-Produktion“ – auf die neue Technologie verlangt den Unternehmen viel ab. „Das ist ein echter Paradigmenwechsel. Da müssen Ökonomen, Maschinenbauer, Chemiker, Juristen, Marketing-Leute, Qualitätssicherer an einem Strang ziehen.“ Und das wagen am Ende nur die Mutigen. In Schaels Projekt geht es also nicht nur darum, Unternehmen optimierte Verfahren zu liefern, sondern auch gemeinsam zu erarbeiten, wie der technologische Wandel transdisziplinär angepackt werden kann. Auch da ist es dann wichtig, dass die Chemie stimmt.
Kontakt
Christina Janssen
Hochschulkommunikation
Tel.: +49.6151.16-30112
E-Mail: christina.janssen@h-da.de