Nachhaltige Kunststoffproduktion
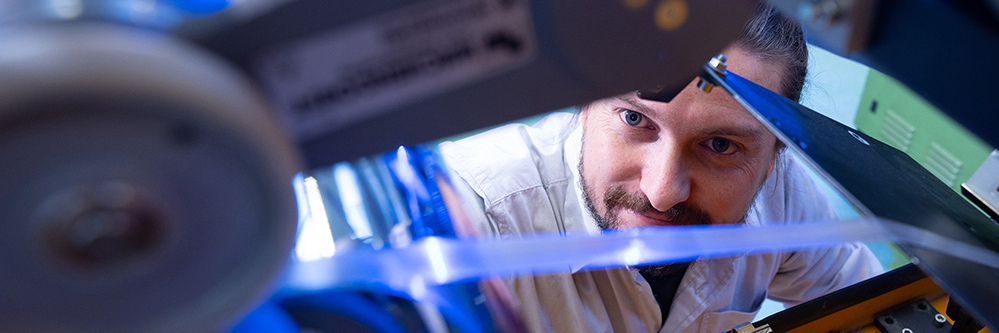
Bei Kunststoff denken heute viele zu allererst an Plastikmüll. Dabei ist Kunststoff viel mehr: Ohne ihn gäbe es keine Touchscreens, Handys, LED-Lichttechnik und während der Corona-Pandemie keine schnelle Impfstoffentwicklung oder FFP2-Masken. Wie nachhaltig und umweltschonend Kunststofftechnologie sein kann, beweisen junge Forschungsteams um Professor Jürgen Wieser am Fachbereich Maschinenbau und Kunststofftechnik der Hochschule Darmstadt gleich in mehreren Projekten. Dabei gelingt der Spagat zwischen Praxisnähe und Grundlagenforschung.
Von Astrid Ludwig, 6.11.2024
Das war mal die Türverkleidung eines Autos. Jetzt sind davon nur noch klein geschredderte, braungraue Brösel übrig – braungrau deshalb, weil sie zu großen Teilen aus Flachs bestehen. Naturfaserverstärkte Kunststoffe wie Flachs-Polypropylen ersetzen in der Automobilindustrie und im Flugzeugbau schon seit vielen Jahren erdölbasierte Kunststoffe, meist bei der Ausstattung der Innenräume. „Das Material ist stabil und leicht“, erklärt Heiko Hofmann, wissenschaftlicher Mitarbeiter am Fachbereich Maschinenbau und Kunststofftechnik. Die so genannten Organobleche lassen sich zudem wiederverwerten. Klingt erst einmal gut, doch ihre Aufbereitung ist herausfordernd, so Hofmann.
Das Recycling von Naturfasern hat einen Haken und den kann man riechen. „Flachs hat einen sehr strengen Eigengeruch“, sagt der h_da-Forscher und lässt zum Beweis an der Tüte mit Häckseln schnuppern. Dem Material entströmt ein starkes Aroma nach Holz und Rauch. Beim Whisky mag das ein Qualitätsmerkmal sein, im Innern eines Autos ist eine Ausdünstung, die an Lagerfeuer erinnert, jedoch unerwünscht – und auch nicht zugelassen. Hinzu kommt, dass das faserverstärkte Material von geringer Fließfähigkeit ist, sich im Spritzguss also, dem häufigsten Verfahren in der Kunststofftechnik, kaum verarbeiten lässt.
Erfolgreiches Rezept
Heiko Hofmann und sein Team aus Mitarbeitenden und Studierenden haben sich dieser Probleme zwei Jahre lang in einem Forschungsvorhaben angenommen. Mit finanzieller Unterstützung von rund 212.000 Euro aus dem „Zentralen Innovationsprogramm Mittelstand“ des Bundesministeriums für Wirtschaft und Klimaschutz (BMWK) und in Zusammenarbeit mit dem Unternehmen Graupner entwickelten sie ein neuartiges Verfahren für die Aufbereitung des recycelten Naturfaserstoffes.
Hofmann, der eine Ausbildung als Industriemechaniker absolvierte und sich vom Hauptschulabschluss bis zu Fachabitur und Studium hocharbeitete, ließ nicht locker. Er mischte dem gehäckselten Material ein Schleppmittel bei, das im anschließenden Verarbeitungsprozess mit Hilfe eines Vakuums wieder herausgefiltert wurde. Mittels „Fließverbesserern“ ließ sich aus dem unregelmäßigen Häckselmaterial ein fester Rezyklat-Strang gewinnen, der zu einem gleichförmigen und vor allem auch geruchsarmen Granulat verarbeitet werden kann.
„Wir haben sogar die Zulassung durch ein Prüfinstitut bekommen“, berichtet Hofmann. „Der Prozess und die Rezeptur stehen.“ Das beteiligte Unternehmen kann die h_da-Rezeptur für die Entwicklung neuer Automobilteile anwenden. Für Jürgen Wieser, der als Professor am Institut für Kunststofftechnik der h_da das Projekt betreut, ist das nicht nur ein Beleg für die Stärke einer Hochschule für Angewandte Wissenschaften. Es ist auch „ein Erfolg und Beitrag für mehr Nachhaltigkeit und den Einsatz von hochwertigem Recyclingmaterial.“
Schwankungen bei der Dosierung verhindern
Wie so oft, ist die richtige Dosis entscheidend. Die Inhaltsstoffe müssen in einem bestimmten Verhältnis zueinander stehen. Kunststoff wird in der Regel in kontinuierlichen Prozessen verarbeitet, bei denen mehrere zusammenfließende Stoffströme so abgestimmt werden müssen, dass ein gleichförmiges Produkt entsteht. Anders als beim Backen werden die einzelnen Bestandteile nicht einzeln abgewogen und nacheinander in einen Mischbehälter gegeben. Die Zusammensetzung der Mischung muss zu jedem Zeitpunkt genau passen, weil sonst auch das kontinuierlich entstehende Produkt in der Zusammensetzung schwanken würde. Die Herausforderungen sind schon bei pulverförmigen Rohstoffen groß, besonders schwierig wird es bei Mahlgut, Fasern oder Flakes wie etwa Folienschnipseln, wie sie typischerweise in Recyclingprozessen vorkommen, erklärt Ivan Kibet, wissenschaftlicher Mitarbeiter am Fachbereich und Doktorand am Promotionszentrum Nachhaltigkeitswissenschaften der h_da.
Doch was genau passiert bei der Dosierung und wieso kommt es manchmal bei vermeintlich identischen Rohstoffen zu unterschiedlichem Verhalten? Eine Frage, mit der sich fast alle Produkthersteller herumschlagen – nicht nur in der Kunststoffindustrie, auch in der Bau-, Automobil-, Lebensmittel- oder Pharmabranche. „Eine genaue, schwankungsfreie Dosierung in kontinuierlichen Prozessen ist für alle relevant“, betont der h_da-Wissenschaftler. Farbeinstellungen in der Automobilindustrie müssen immer gleich ausfallen, mechanische Eigenschaften eines Bauteiles konstant sein, Medikamente die gewünschte Wirkung entfalten oder Batteriewerkstoffe mit dem korrekten Anteil von Flammschutz-Zusätzen versehen werden. Fehler in der Dosierung können kostenträchtigen, umweltschädlichen Ausschuss produzieren, teure Produktionsausfälle auslösen oder auch das Risiko von vertrauensschädigenden Rückrufaktionen erhöhen.
„Erfahrungswissen ist da, das Verständnis der Zusammenhänge fehlt“
Ein Grund, warum sich 16 Firmen aus der Industrie und die Forschungs-Gesellschaft Verfahrens-Technik an dem Forschungsprojekt „DOSISPEC“ beteiligen. Mit rund 240.000 Euro Drittmitteln wird das Vorhaben aus dem Programm zur Industriellen Gemeinschaftsforschung (IGF) vom BMWK unterstützt. Ziel ist, Grundlagen zur Spezifizierung des Fließ- und Dosierverhalten bestimmter Schüttgüter zu erarbeiten. In vielen Unternehmen basiert das Knowhow über die richtige Dosierung auf langjährigen Erfahrungen. Ändern sich Maschinen, Materialien oder Mitarbeitende, kann es schwierig werden. „Erfahrungswissen ist da, das Verständnis der Zusammenhänge fehlt“, sagt Professor Wieser. Das will das sechsköpfige Projektteam ändern.
Ivan Kibet und sein Team leisten dabei detektivische Arbeit. Sie besichtigen Anlagen der Unternehmen vor Ort, prüfen im Labor die Rheologie – die Fließeigenschaften der Schüttgüter – führen Dosiertests durch und untersuchen unter anderem, welchen Einfluss etwa Luftfeuchtigkeit oder Lagerung auf das Fließ- und Dosierverhalten haben. Herauskommen soll eine Art Handbuch mit Modellen und Empfehlungen zu möglichen Spezifikationen und geeigneten Laborversuchen für die Industriepartner, um vorhersehbarer und umweltfreundlicher zu produzieren.
Mit Grundlagenforschung gegen schwarze, lästige Punkte
Mit einem weiteren, grundlegenden Problem in der Kunststoffverarbeitung befasst sich auch Philipp Seeger, wissenschaftlicher Mitarbeiter am Fachbereich Maschinenbau und Kunststofftechnik, Geschäftsführer des Forschungszentrums Material- und Prozesstechnik der h_da und Doktorand an der TU Clausthal. Seine Forschung dreht sich um so genannte Stippen. Das sind kleine, lästige schwarze Punkte, die als Verunreinigungen oder Fehlstellen in transparenten Kunststoffen immer wieder für Ärger sorgen. Problematisch sind vor allem die Partikel, die während der Weiterverarbeitung des Kunststoffes in den Spritzgussmaschinen oder Extrudern entstehen. Extruder sind Fördergeräte, die mittels rotierender Schnecken, die aussehen wie überdimensionale Schrauben, das feste Material in Schmelze überführen und diese unter hohem Druck und hoher Temperatur gleichmäßig in Form pressen.
Wie es zu diesen Stippen kommt, ist nach wie vor nicht völlig geklärt. Zunächst dachte man, dass die Schmelze auf den heißen Metalloberflächen anbrennt – ähnlich einem Würstchen in der heißen Pfanne. Das Forschungsteam fand jedoch heraus, dass die Realität deutlich komplexer ist. Bei Temperaturen um die 300 Grad lagert sich der Kunststoff, etwa Polycarbonat, in hauchdünnen Schichten an den Wänden der Maschine ab. Diese Schichten sind anfangs wenige Nanometer dick, ein Haar ist fünf- bis zehntausendmal dicker. Dann wachsen diese Beläge weiter an. Irgendwann können sich Teile davon ablösen und landen im Produkt, das damit unbrauchbar wird. „Ein schon sehr altes Problem, aber keiner weiß bisher genau, was bei Wachstum und Ablösung der Schicht genau passiert“, ergänzt Experte Wieser. „Bislang gab es dazu nur Trial-and-Error-Lösungen, ohne wirklich zu wissen, warum irgendeine gewählte Maßnahme hilft.“ Versuche, den schwarzen Punkten mit Oberflächenbeschichtungen entgegenzuwirken, sind in der Praxis üblich, die Lösungsfindung jedoch meist zufallsabhängig und im Einzelfall sehr langwierig. „Das Problem tritt aber immer wieder auf“, berichtet Seeger. Die Ausschussquoten liegen bei bis zu fünf Prozent und manchmal höher. Das Material kann wegen der Verunreinigung nicht wiederverwertet werden. „Wirtschaftlich und umwelttechnisch ist das ein großes Thema“, so der Wissenschaftler.
Kooperation mit der Uni Clausthal und zahlreichen Unternehmen
Gemeinsam mit dem Zentrum für Materialforschung der Universität Clausthal, das auf Oberflächenphysik spezialisiert ist, konnte die Darmstädter Forschungsgruppe Wechselwirkungen des Materials mit der Metallwand der Maschinen aufzeigen. Dabei diffundieren Eisen-Ionen in den Kunststoff und verändern ihn, berichtet Philipp Seeger. „Nun schauen wir uns den Prozess genauer an, stellen die Strömungsbedingungen nach und erforschen die zeitliche Entwicklung der Beläge.“ Dafür haben sie eigens einen Hybrid aus Spritzgussmaschine und Extruder entwickelt, in den auch ein Kamerasystem und ein Laser eingebaut sind. Damit sollen in der Schmelze die Stippen entdeckt und anschließend dokumentiert werden. „Wir sehen dann genau, ob und was sich verändert, wenn wir die Parameter ändern.“ Auch hier sind zahlreiche Partner aus der Kunststoffbranche, der metallverarbeitenden Industrie sowie Beschichtungsunternehmen über das IGF-Programm des Bundes mit im Boot. Rund eine halbe Million Euro stehen bis 2026 für diese Grundlagenforschung zur Verfügung. Die Erkenntnisse aus dem Labor werden in der Praxis helfen, gezielte Lösungen zu entwickeln, hofft er. Dadurch ließen sich dann deutlich Ressourcen einsparen.
Die drei Projekte zeigen, wie die Forschung an Kunststoffen zur Nachhaltigkeit beitragen kann. Die h_da-Forscher sind überzeugt: „Kunststoff steht derzeit stark in der Kritik, aber ohne ihn wird es nicht gehen. In unseren Projekten arbeiten wir daran, die Abfallquoten zu senken, die Verarbeitung zu optimieren sowie die gesamten Prozesse umweltfreundlicher zu machen.“
Kontakt zur h_da-Wissenschaftsredaktion
Christina Janssen
Wissenschaftsredakteurin
Hochschulkommunikation
Tel.: +49.6151.533-60112
E-Mail: christina.janssen@h-da.de
Fotografie: Markus Schmidt