Materialforschung
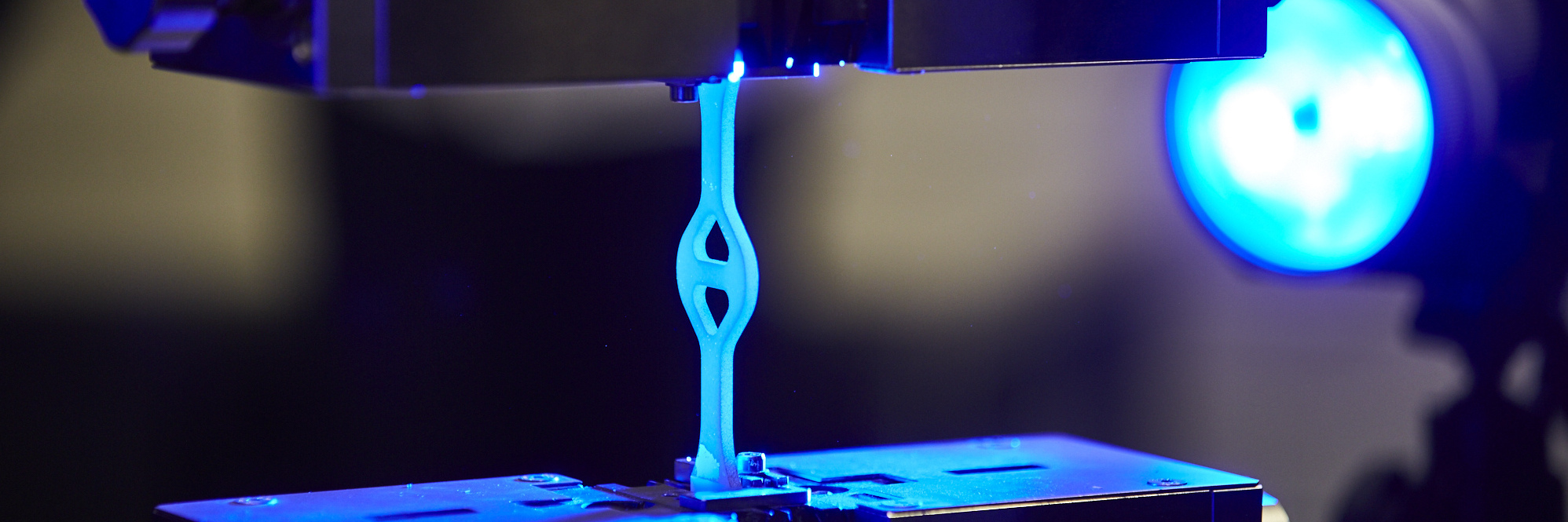
An der Hochschule Darmstadt (h_da) hat sich eine Gruppe von Forschenden unterschiedlicher Fachrichtungen im Forschungszentrum Material- und Prozesstechnik zusammengetan, um die Entwicklung von Kunst- und Baustoffen auf eine nachhaltigere Basis zu stellen. Das Anwendungsspektrum reicht von Wurstverpackungen und Klebeverschlüssen über Bauteile für Flugzeuge bis hin zum Tiefbau mit Leichtbeton. Für die internationale Vernetzung auf diesem Gebiet erhielt die Gruppe bereits eine Förderung der Deutschen Forschungsgemeinschaft (DFG). Ein gemeinsames Projekt wurde vom Land Hessen als eines der besten im Rahmen des Förderprogramms Distr@l ausgezeichnet.
Von Christina Janssen, 20.4.2024
Was haben ein Flaschendeckel und ein Flugzeug gemeinsam? Fliegen kann der Deckel jedenfalls nur, wenn er geworfen wird. Beide Produkte bestehen allerdings aus Kunststoff: der Deckel aus Polypropylen, moderne Flugzeuge zu einem großen Teil aus ultraleichten Verbundstoffen. Solche Kunststoffe sind aus dem Alltag nicht wegzudenken: Surfbretter und Medizinprodukte, Mikrochips und Käseverpackungen, Bauteile für die Luft- und Raumfahrt – die Liste ließe sich beliebig fortsetzen. „Der Kunststoff begleitet uns durch den ganzen Tag“, bringt es Dr. Alexander Knieper vom Fachbereich Maschinenbau und Kunststofftechnik der h_da auf den Punkt.
Weil das in vielen Bereichen so bleiben wird, haben sich Forschende aus drei Fachbereichen der Hochschule Darmstadt zu einer interdisziplinären Gruppe zusammengeschlossen: die Mathematikerin Prof. Dr. Romana Piat mit ihren Doktoranden Pascal Happ und Vinit Deshpande, die Kunststofftechnik-Experten Prof. Dr. Martin Moneke, Prof. Dr. Roger Weinlein und Dr. Alexander Knieper sowie Bauingenieur Prof. Dr. Albrecht Gilka-Bötzow. Gemeinsam forschen Sie daran, die Produktion von Kunststoffen zu optimieren und Wertschöpfungsketten nachhaltiger zu gestalten. Auch Baustoffe wie den Leichtbeton hat die Gruppe im Blick. Im Kern geht es darum, neue Materialien virtuell numerisch zu designen. „Wir modellieren neue Materialien am Rechner“, erklärt Mathematik-Professorin Piat. Aufwändige Tests, die sonst im Labor gemacht werden müssten, werden dadurch zu einem großen Teil verzichtbar. „Das spart Zeit, Material und Energie.“
Kreide statt Krankmacher
Bei der Entwicklung neuer Werkstoffe geht es in der Regel darum, das Material durch die Beimischung von Zusatzstoffen, sogenannten Additiven, für spezifische Anwendungen zu optimieren. Der Mix muss perfekt stimmen, die Rezeptur exakt auf die jeweilige Anwendung zugeschnitten sein: Durch den Zusatz von Fasern gewinnen Kunststoffe an Belastbarkeit, durch Metallpartikel werden sie leitfähig, durch UV-Blocker langlebiger. Kunststoff-Ingenieur Martin Moneke beschreibt ein Beispiel: „In einem unserer letzten Projekte ging es darum, das weiße Pigment Titandioxid in einem Kunststoff zu ersetzen, weil es eine Zeitlang im Verdacht stand, gesundheitsschädlich zu sein.“ Gleichzeitig sollten die mechanischen Eigenschaften des Kunststoffs verbessert werden. In diesem Fall experimentierten Piat und Moneke mit weißen Kreidepartikeln, die der Kooperationspartner Granula Polymer dem Kunststoff ersatzweise beimischte. „Wir simulieren in solchen Fällen das Verhalten des neuen Materialmixes durch numerische Modelle am Rechner und treffen dann Vorhersagen über seine Eigenschaften“, erläutert Romana Piat, die vor ihrem Wechsel an die h_da im Jahr 2015 am Karlsruher Institut für Technologie (KIT) forschte. Um derlei Berechnungen anstellen zu können, analysieren Piat und ihr Team die Geometrie der einzelnen Kunststoff-Bestandteile anhand von mikroskopischen und mikrotomographischen Aufnahmen. „Wir ‚zoomen‘ in das Material hinein und schauen uns die Mikrostruktur genau an. Die Rede ist hier also von Mikropartikeln, die so fein sind wie Pulver, oder Fasern, die dünner sind als ein menschliches Haar.“
Doch wie nah kommt die Simulation an die Realität heran? Das zeigen erst die Materialtests in den Kunststofftechnik-Laboren der h_da. Auf Grundlage der Testergebnisse wird das Simulationsmodell dann evaluiert, nachgebessert, der Kunststoff-Mix neu gemischt und erneut im Labor getestet. „Wir kennen vorab die Eigenschaften der einzelnen Bestandteile hinsichtlich Steifigkeit, Schmelzpunkt, Rauigkeit, Partikelgröße und so weiter“, erläutert Professor Gilka-Bötzow die Vorgehensweise. „Doch wie sich diese Eigenschaften verändern, wenn man die einzelnen Bestandteile mischt, lässt sich nicht exakt voraussagen.“ So entstehen neue Materialien im Zusammenspiel zwischen mathematischen Modellierungsschleifen und Testreihen im Labor.
Betonklotz reloaded
Ein System, das sich auf den Baustoff Beton übertragen lässt. Dabei muss hier wohl nicht an die einschlägige Filmszene aus Ein Fisch namens Wanda erinnert werden, um das prototypische Bild eines „Betonklotzes“ wachzurufen. Nicht aufgrund cineastischer Grausamkeit, sondern aus Gründen der Nachhaltigkeit soll aus dem Schwergewicht ein Leichtgewicht werden: „Hochbauten können inzwischen aus vielen alternativen Materialien hergestellt werden“, beschreibt Bauingenieur Gilka-Bötzow die Ausgangslage. „Tatsächlich ist das aber beim Tiefbau nicht der Fall, weil diese Gebäudeteile in der Erde sind und mit Wasser in Berührung kommen. Dort ist der Beton weitgehend alternativlos.“ Ergo: Kein Holzhochhaus ohne Betonfundament.
Der Beton soll also leichter werden, aber die gewünschte Tragfähigkeit und Beständigkeit behalten. Optimiert wird dafür unter anderem die Gesteinskörnung in den Betonmischungen – mit ähnlichen Methoden wie beim Kunststoff: „Als Menschen sehen wir nur die Makro-Ebene, also den Betonklotz“, erläutert Gilka-Bötzow. „Im Labor zoomen wir auch hier in die Betonmischungen hinein, schauen auf die Mikro-, Meso- und Makro-Ebene – und kombinieren dann Simulation mit Labortests.“ Früher habe es oft viele Jahre gedauert, bis neue Materialien zum Einsatz gekommen seien, sagen die Forschenden. Dieser Prozess beschleunigt sich nun immens – durch die Kombination von numerischer Mathematik und Kunststofftechnik.
Parship für Plastik
In anderen Projekten greifen die Expertinnen und Experten in die Trickkiste der Kunststofftechnik, um sehr spezielle Kunststoff-Verbindungen zu ermöglichen: „Für die Folienverpackungen von Wurst oder Käse, die Klebeverschlüsse an Windeln oder auch bestimmte Leitungssysteme in Autos müssen Kunststoff-Schichten miteinander verbunden werden, die sich eigentlich – wie Wasser und Öl – nicht gerne mischen“, berichten Dr. Alexander Knieper und Professor Roger Weinlein. Gemeint sind Polypropylen und Polyamid. Um sie zu mehrschichtigen Folien zu verbinden, mischten die Wissenschaftler der Polypropylen-Schicht polare Substanzen bei, die als „Kompatibilisatoren“ wirken, also wie Seife für Öl und Wasser. „Hierdurch entsteht auf der Oberfläche elektrische Ladung, sodass die beiden Schichten aneinander haften“, erläutert Alexander Knieper.
In einem weiteren Projekt in Kooperation mit dem Familienunternehmen Granula Polymer aus dem hessischen Groß-Umstadt ging es darum, Polypropylen und Polyamid zu Bauteilen zu verbinden, um die jeweiligen Vorteile der beiden Polymere in einem Bauteil zu kombinieren. In diesem Fall wurde dem Polypropylen eine reaktive Substanz beigemischt, die sich mit dem Polyamid verbindet. So entstanden an der Grenzschicht starke Bindungen und eine Kombination der beiden unterschiedlichen „Kunststoffe“ wurde möglich.
Von den so hergestellten Test-Objekten erstellten Professorin Piat, Pascal Happ und Vinit Deshpande einen digitalen Zwilling. „Dabei ging es zuerst darum zu testen, ob unsere Simulation widerspiegelt, wie sich das Material in Wirklichkeit verhält“, berichtet Doktorand Pascal Happ. In weiteren Schritten konnte das Team dann simulieren, wie sich die mechanischen Eigenschaften des Verbundmaterials ändern, wenn man an einzelnen Stellschräubchen dreht und die Rezeptur verändert. „Das Ziel ist auch hier, schneller und nachhaltiger zu Ergebnissen zu kommen“ fasst Kunststoffexperte Weinlein zusammen.
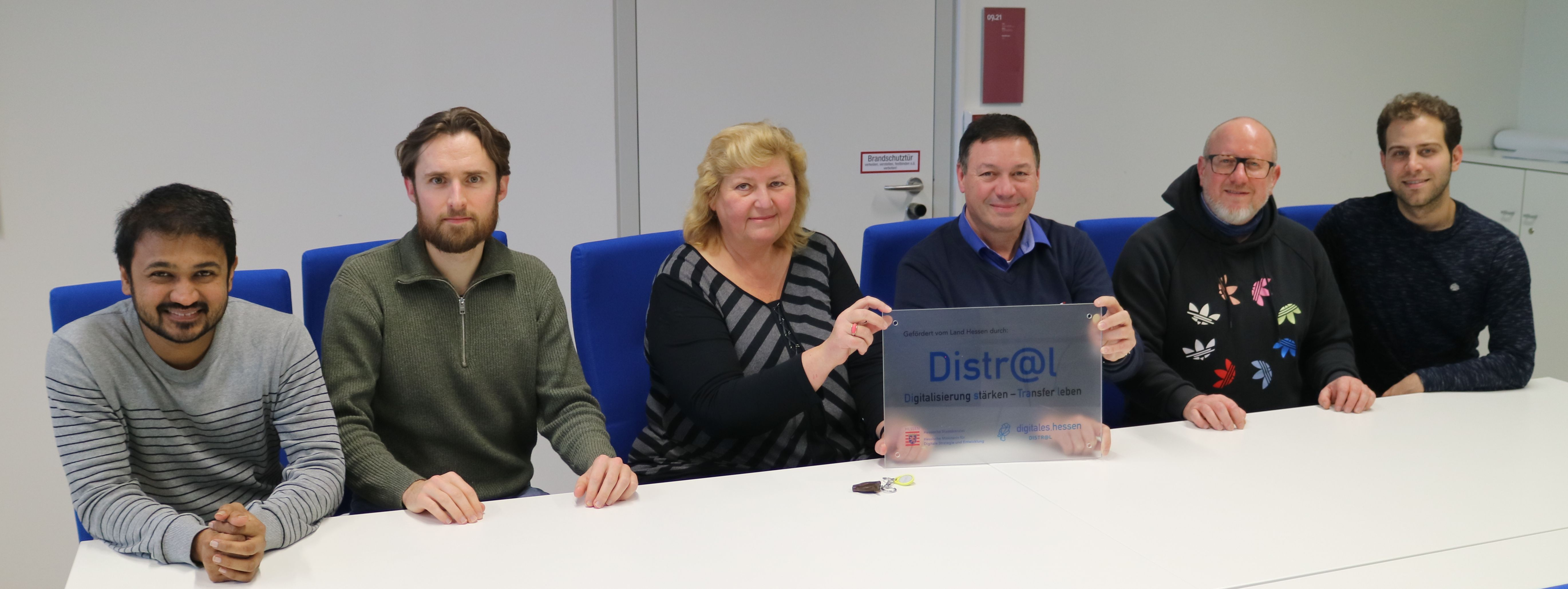
Für die Projektpartner aus der Industrie haben solche Kooperationen einen großen Nutzen. „Prodzierende Unternehmen haben meist keine eigenen Spezialisten im Bereich Modellierung oder Numerik“, erläutert Romana Piat. „Deshalb haben wir unsere Software sehr benutzerfreundlich entwickelt.“ Das heißt praktisch: Das Unternehmen bekommt eine Auswahl von Materialien und erstellt dann mit Hilfe der Software Vorhersagen, welche davon gut zusammenpassen könnten. Eine Art Parship für Kunststoffe. Das Projekt wurde vom Hessischen Ministerium für Digitalisierung im Rahmen des Programms Distr@l gefördert und in der abschließenden Evaluation mit dem Qualitätssiegel in Gold ausgezeichnet.
Aufbau internationaler Kooperationen
Um die gemeinsame Forschung auf eine breitere Basis zu stellen, strebt das h_da-Team an, sich international stärker zu vernetzen. Im Rahmen eines von der DFG geförderten Projekts zum Aufbau internationaler Kooperationen organisierte Romana Piat deshalb im Winter einen hochkarätig besetzten Workshop mit Teilnehmenden aus Deutschland, den USA und Schottland. Das Treffen in Darmstadt, das vom Forschungszentrum Material- und Prozesstechnik der h_da mitfinanziert wurde, ist nun Ausgangspunkt für gemeinsame Vorhaben auf internationaler Ebene: Die Gruppe will den fachlichen Austausch intensivieren, plant derzeit weitere Workshops und erste gemeinsame Anträge für Drittmittelprojekte.
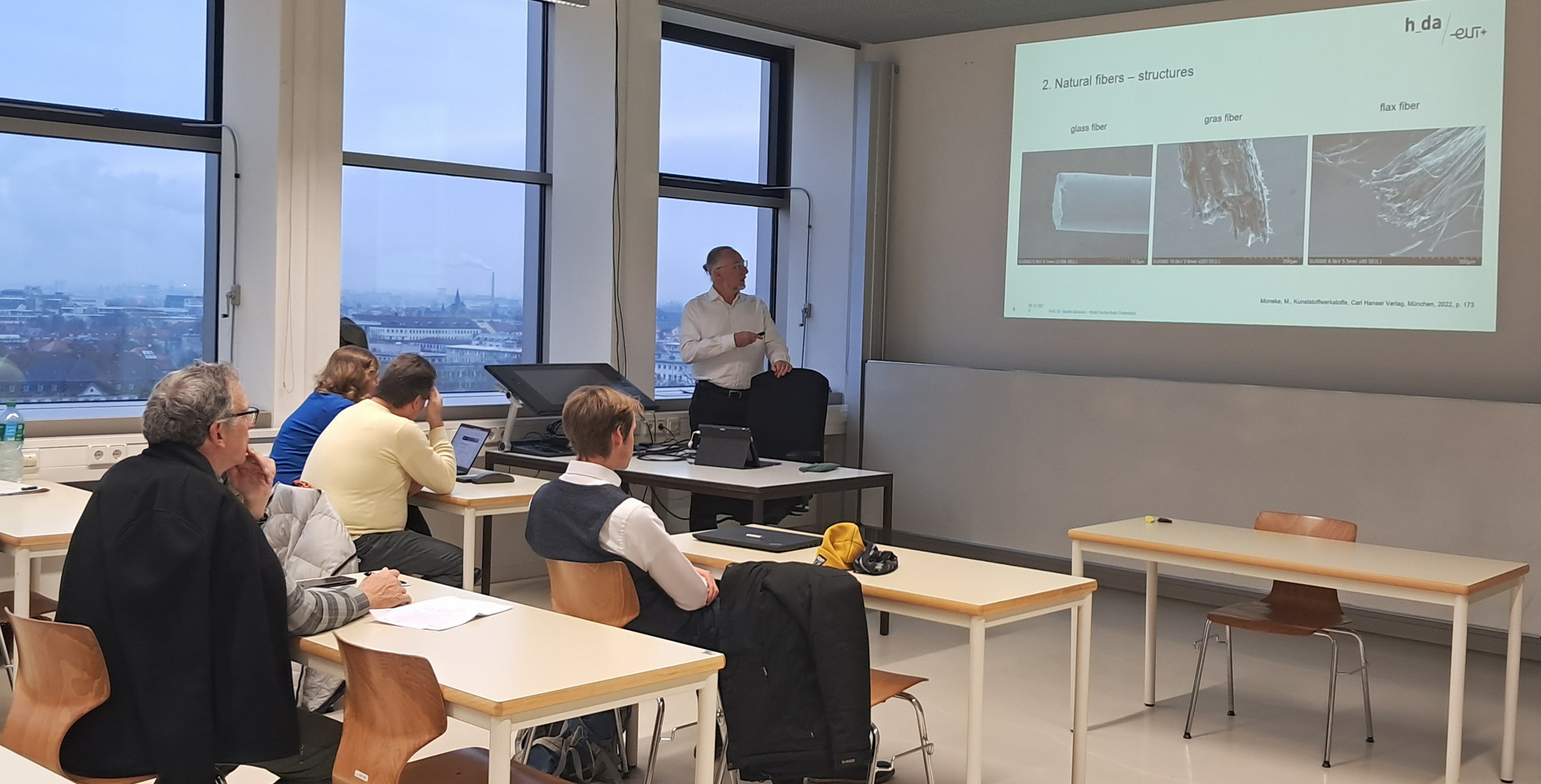
Davon sollen auch die Studierenden profitieren. Spannende Forschungsprojekte wollen die Wissenschaftlerinnen und Wissenschaftler auch dazu nutzen, Neugier und Begeisterung für ihr Fachgebiet zu wecken. Denn Absolventinnen und Absolventen aus den Bereichen Kunststofftechnik, Mathematik und Bauingenieurwesen werden auf dem Arbeitsmarkt händeringend gesucht – und müssen sich fürs Erste gewiss nicht die Frage stellen, ob ihre Arbeitsplätze durch „KI“ bedroht sind. Fragt man übrigens ChatGPT nach den gemeinsamen Eigenschaften von Flaschendeckel und Flugzeug, lautet die erste Antwort: „Beide können dazu verwendet werden, etwas abzudichten oder zu verschließen.“
Kontakt zur h_da-Wissenschaftsredaktion
Christina Janssen
Wissenschaftsredakteurin
Hochschulkommunikation
Tel.: +49.6151.533-60112
E-Mail: christina.janssen@h-da.de
Infos zu den Studiengängen
Das Forschenden-Team der h_da
Website Prof. Dr. Gilka-Bötzow
LinkedIn-Seite Prof. Dr. Martin Moneke
Website Prof. Dr. Romana Piat
Website Prof. Dr. Roger Weinlein
Dr. Alexander Knieper
Pascal Alexander Happ
Vinit Vijay Deshpande