Innovative cleaning concept for aircraft engines
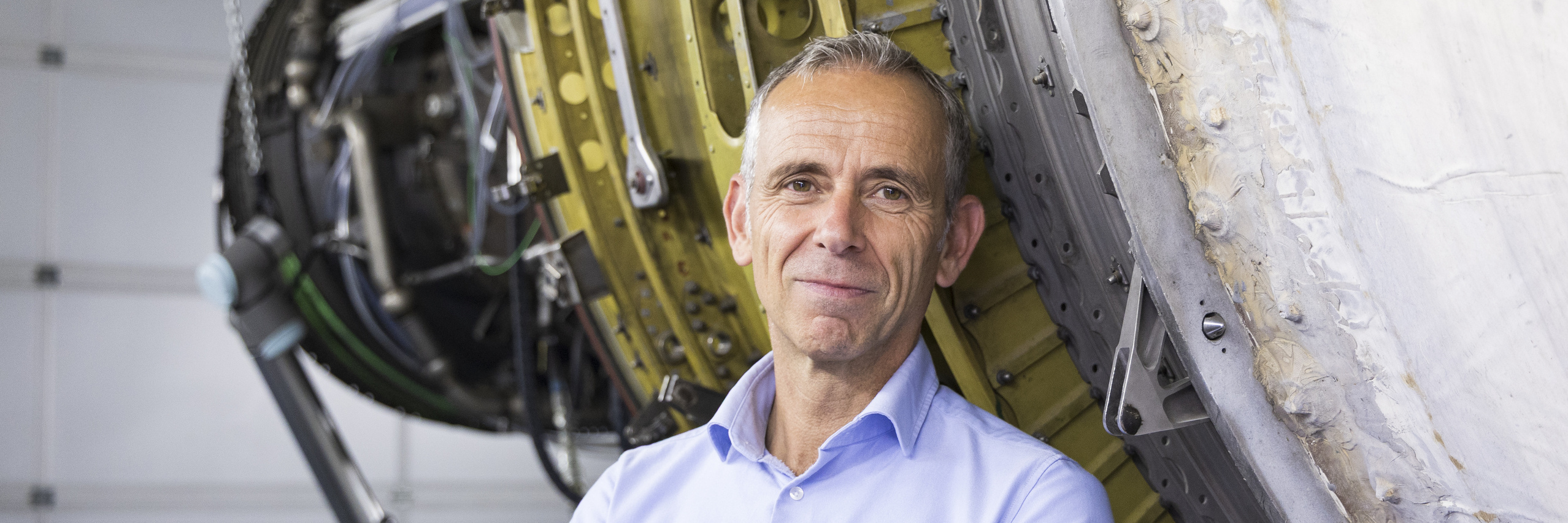
Even wafer-thin layers of dirt can have a big impact. When dirt settles on the blades of aircraft turbines, it leads to higher consumption of jet fuel and more emissions, as well as shortening the service life of costly components. That is why researchers at Darmstadt University of Applied Sciences (h_da) have been working successfully with Lufthansa Technik AG for many years on new, environmentally friendly and time-saving processes for cleaning aircraft turbines. In his latest research project, Professor Gerald Ruß and his team have developed an innovative cleaning process for the hot gas section, i.e. the combustion chamber and the turbine, of civil aircraft. The Federal Ministry for Economic Affairs and Energy funded the project, and the researchers are now preparing to file a patent for their invention.
By Astrid Ludwig, 4.7.2025
Although the blades are rather unspectacular, in fact just a few centimetres in size, they are incredibly expensive. Professor Gerald Ruß, an expert in engines, machines and thermal engineering at h_da’s Faculty of Mechanical and Plastics Engineering, is holding one in his hands. “New ones cost several thousand euros each,” he says. Around 70 of them are installed in the rotating part of a turbine stage of an aircraft engine, through which the hot exhaust air from the combustion chamber flows and produces thrust. This means that almost €1m worth of these components alone are installed in a single turbine. It is the special metal alloy, the shape and the coating that make these hand-sized items so special and costly.
Own turbine hall
You can find Professor Ruß in Building C18 on h_da’s Schöfferstraße Campus. The turbine test bench was built in 2011 specifically for research projects. Teams of scientists at the university have been working together with Lufthansa Technik AG since the early 2000s. Three consecutive research projects to date have explored various innovative methods for cleaning turbines. The starting point for this collaboration was a thesis written in 2005: “Back then, our student Sebastian Giljohann developed an idea for a water-based process for turbine cleaning,” says Gerald Ruß. The collaboration between scientists and students at h_da and engineers at Lufthansa Technik AG then took its course. The Lufthansa subsidiary offers maintenance, repair and overhauling services and has a facility at Frankfurt Airport. Cleaning processes co-developed by h_da are already in use worldwide.
The third joint research project has been running successfully since 2018. The Federal Ministry of Economic Affairs and Energy funded the project entitled “Development of a cleaning model for innovative cleaning processes for the hot gas section of civil aircraft turbines” – the official title, which is abbreviated to HSC – for four years with almost €2m, of which €1.1m went to h_da. This time too, the researchers at h_da are working on original components and under real operating conditions: the turbine test bench accommodates the jet engine of a Boeing 747-200, which was in regular service with various airlines for many years. Ruß, who previously worked for a jet engine manufacturer and has good contacts in the industry, was able to arrange the purchase of the decommissioned engine for the university. Its size is impressive. The component, which exposes the different parts of the engine, weighs almost four tons, is 4.65 metres in length and 2.44 metres in diameter. It occupies almost the whole test bench.
The huge fan dominates the front view. It draws in the air needed for the turbine to operate. “In just one second, air volume is about the size of a house,” says Professor Ruß to illustrate the vast amount of air involved. However, not only air is sucked into the engine but also dust, pollen, ash, exhaust fumes and sand – “depending on the location, the flight route or how close the engine is to the ground,” explains Ruß. If the dirty air enters the combustion chamber and the turbine, where temperatures of over 1000 °C prevail, the particles melt and settle as a thin film on the surface of the blades. “This changes the aerodynamics and the degree of efficiency, as well as increasing fuel consumption, which in turn increases emissions and shortens the parts’ service life,” he explains.
Cleaning the hot section
That is why the turbines in normal civilian flight operations have to be maintained and cleaned at regular intervals and depending on the flight route. For the airlines, this is time-consuming and costly, above all when it comes to cleaning the combustion chamber, high-pressure turbine, low-pressure turbine and fuel nozzle – known collectively as the “hot section”. It is precisely this section that the university’s latest research project with Lufthansa Technik AG is spotlighting. “To date, it has only been possible for airlines to clean the hot section during a major – and expensive – inspection, when the aircraft is taken out of service and the engines have to be dismounted from the wings,” explains Ruß. The aim of h_da’s research, by contrast, is to conduct maintenance work and cleaning during a normal, smaller check, where the engine can remain in situ – in other words, under “on-wing conditions”. “If this is successful, it will really pay off for airlines,” says Ruß.
However, the components in the hot section are difficult to access. That is why the researchers working on the project have focused specifically on cleaning the hot section via the inspection openings, in this way circumventing the complex dismounting of components and cladding. The inspection openings are around eight to ten openings that resemble palm-sized screws. “The art lies in injecting the cleaning agent through these openings,” says Ruß. As this is difficult to do by hand, his research team has designed and programmed a robotic arm to do the cleaning automatically.
A concept with potential
“We looked into numerous cleaning options,” he reports. These included cleaning with high energy light beams, lasers, water, dry ice or plasma jets. The h_da team evaluated which methods or possibly combinations of cleaning methods are effective and whether they perhaps damage components in the process. “We have developed a concept that shows potential,” says Professor Ruß. “Our method produced promising results in the first test under realistic conditions.” It would be one of the first processes of its kind in commercial aviation. For reasons of confidentiality, however, he is not allowed to disclose details, as the possibility of filing a patent is currently under review.
What he does reveal is that the actual cleaning process takes no more than 20 minutes, meaning that the engine and the aircraft could go back into operation much faster than has been the case so far. That would be a huge step forward and save a lot of time for the airline. In this way, it would be possible to clean turbines more often and more easily, and they would be cleaner and more economical. Clean engines consume less fuel. “This would mean a reduction in carbon emissions of several hundred thousand tons per year for an airline like Lufthansa,” says Ruß. Which is why, in his opinion, such application-oriented research at h_da makes an important contribution to environmental and climate protection.
Contact the impact Editorial Team
Christina Janssen
Science Editor
University Communications
Tel.: +49.6151.533-60112
Email: christina.janssen@h-da.de
Translation: Sharon Oranski
Photography: Samira Schulz